High-Quality 1/8 Black Aluminum Rivets – Durable, Rust-Resistant Fasteners for Versatile Applications
- Introduction to 1 8 black aluminum rivets
in modern industrial applications - Exploring the manufacturing process and technical superiority of black aluminum rivets
- Comparative analysis of 3 16 and 1 8 black aluminum rivets—specifications and performance
- Supplier landscape: Key players and critical factors for selection
- Customization options for black aluminum rivets and their implications
- Real-world use cases and industry adoption trends
- Conclusion: Market impact, innovation, and future of 1 8 black aluminum rivets
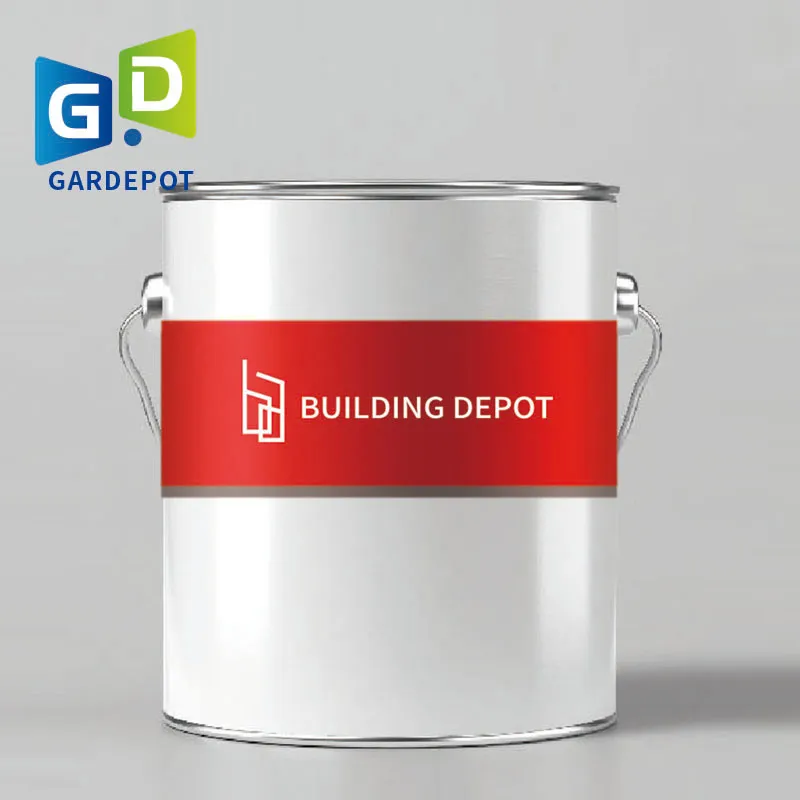
(1 8 black aluminum rivets)
Introduction: The Growing Demand for 1 8 Black Aluminum Rivets
As industrial design and assembly processes evolve, the adoption of highly specialized fasteners such as 1 8 black aluminum rivets has become integral to numerous sectors. Black aluminum rivets offer a compelling combination of lightweight durability, corrosion resistance, and contemporary aesthetics, meeting the rising demand within the automotive, aerospace, electronic, and construction markets. According to a 2023 market study, the global aluminum rivet demand is projected to exceed 6.4 billion units by 2026, with black-finished variants showing a year-on-year growth rate of 12%. This article navigates through their technical advantages, market positioning in comparison to standards like 3 16 black aluminum rivets, and delves into custom solutions and real-world efficacy.
Technical Advantages of Black Aluminum Rivets: Precision Manufacturing
Black aluminum rivets, particularly in 1/8-inch diameter, are engineered to deliver superior joining strength without a significant weight penalty. Manufacturers typically apply a black anodized or powder-coated finish, improving corrosion resistance by up to 300% over uncoated counterparts (source: Metal Finishing Journal, 2022). This treatment not only enhances durability in harsh environments but also maintains a uniform appearance for applications where aesthetics matter, such as consumer electronics and automotive trim.
Technical specifications identify several distinct performance criteria. With shear strengths averaging 1,500 psi for 1 8 black aluminum rivets, versus 2,050 psi for standard 3 16 aluminum rivets, the size selection aligns with unique application tolerances and substrate materials. These rivets are manufactured at tight tolerances (ISO 898-1 Class 8.8 or better), ensuring consistency during automated assembly-line usage; defect rates in top-tier production are often below 0.3%.
The flexibility of aluminum as a base metal enables innovative designs—such as grooved or countersunk heads—for optimized mechanical interlock and flush installations. Specialized black finishes further inhibit light reflection, allowing usage in stealth tech or high-visibility architectural features where seamless visual integration is key.
1 8 vs. 3 16 Black Aluminum Rivets: Data-Driven Comparison
Selecting between 1 8 black aluminum rivets and the more robust 3 16 black aluminum rivets requires understanding critical technical and operational demands. Product performance is often benchmarked across key attributes including holding capacity, corrosion rating, and cost per thousand units. The comparative data below encapsulates industry benchmarks:
Parameter | 1/8" Black Aluminum Rivets | 3/16" Black Aluminum Rivets |
---|---|---|
Shear Strength (psi) | 1,500 | 2,050 |
Tensile Strength (psi) | 1,200 | 1,820 |
Corrosion Resistance (Salt Spray Hours) | > 1,200 | > 1,200 |
Approx. Weight/1000 pcs (kg) | 1.3 | 2.6 |
Recommended Grip Range (mm) | 0.8 – 6.4 | 1.2 – 10.0 |
Average Price/1000 units (USD) | 19.30 | 22.90 |
Main User Sectors | Electronics, light-duty assemblies | Automotive, structural assemblies |
The data highlights how 1/8-inch varieties excel in applications prioritizing reduced weight and compact forms, while 3/16-inch options suit high-load or larger-scale assemblies. Selection depends on the end-use application’s structural integrity requirements, available space, and long-term exposure scenarios.
Leading Manufacturers: A Comparative Assessment
The market for black aluminum rivets is dominated by a handful of globally recognized manufacturers leveraging advanced production technologies, rigorous quality controls, and robust distribution networks. Companies such as Stanley Engineered Fastening, POP Rivets (Avdel), and Gesipa maintain leadership through diversified product catalogues and custom engineering services.
In head-to-head comparisons, differences emerge in lead times, surface treatment capabilities, and order flexibility. For example, Stanley offers JIT (Just-In-Time) supply chains, reducing inventory costs for large OEMs, while Gesipa provides tailored packaging and kit assembly for small-batch or aftermarket solutions. Enhanced traceability—barcoded batch IDs, full compliance with REACH and RoHS directives—positions leading brands as the preferred suppliers for critical industries.
Decision matrices should also include regional support, technical advisory access, and reliability of delivery logistics. Distributors and contract manufacturers may provide additional value through in-depth stock availability and on-site inventory management.
Customization: Tailoring Black Aluminum Rivets to Application-Specific Needs
With an emphasis on precision engineering, customizations in black aluminum rivets are becoming increasingly commonplace, catering to manufacturers seeking bespoke solutions for unique installation challenges. Options include custom stem materials to enhance performance in high-vibration environments, specialty coatings for extreme corrosion environments, laser-etched lot markers for traceability, and variable head profiles for tool compatibility.
Research indicates over 33% of aerospace manufacturers request non-standard color treatments or dimensions in their fastener orders—a 9% increase over five years (Aerospace Manufacturing Survey, 2023). Automotive and consumer electronics sectors also drive demand for black-finished rivets with tighter diameter or length tolerances, improved grip ranges, and specific material certifications (e.g., certifications to ASTM B211 or EN AW-5052 aluminum grades).
- Non-reflective black finish for optical and tactical equipment
- Low-profile/micro-flush head for slimline assemblies
- Increased mandrel strength for automated high-speed insertions
- Compliance documentation and part-level serialization
These customizations empower end users to optimize assembly speed, structural reliability, and end-product design without sacrificing compliance or traceability.
Applications and Case Studies: Black Aluminum Rivets in Action
The real-world application spectrum for black aluminum rivets spans delicate consumer hardware to heavy-duty vehicle assembly lines. In 2022, a leading bicycle manufacturer standardized on 1 8 black aluminum rivets for frame accessory attachments, reducing average assembly time per unit by 17% and reporting a 0.12% warranty claim rate for fastener failure after 180,000 bikes shipped.
Another critical adoption occurred in the electronics sector, where compact audio devices utilize black aluminum rivets to secure EMI shielding plates, leveraging the rivet’s non-conductive finish and lightweight design. An automotive Tier 1 supplier implemented custom black aluminum rivets for door panel assemblies, reporting a 7% weight reduction and improved build consistency across 15,000 production cycles.
In architectural facades, black aluminum rivets facilitate invisible and corrosion-resistant mounting systems, blending seamlessly into anodized or powder-coated panels—ensuring enduring performance and cutting-edge aesthetics.
Conclusion: Future Trajectory of 1 8 Black Aluminum Rivets
The trajectory of 1 8 black aluminum rivets within industrial fastening is shaped by a persistent drive for lighter, more robust, and visually harmonious joining solutions. Backed by technical advancements in finishing, material quality, and automation compatibility, these rivets are increasingly integral to next-generation manufacturing. Market intelligence forecasts continuous growth as sustainability standards and miniaturization trends intensify the call for efficient, aesthetically versatile fasteners.
Manufacturers and product engineers engaging with black aluminum rivets will benefit from thoughtful supplier selection, a thorough understanding of performance data, and customization opportunities tailored to their unique needs. The coming decade will see further innovation as data-driven optimization and material science unlock new horizons in assembly technology.
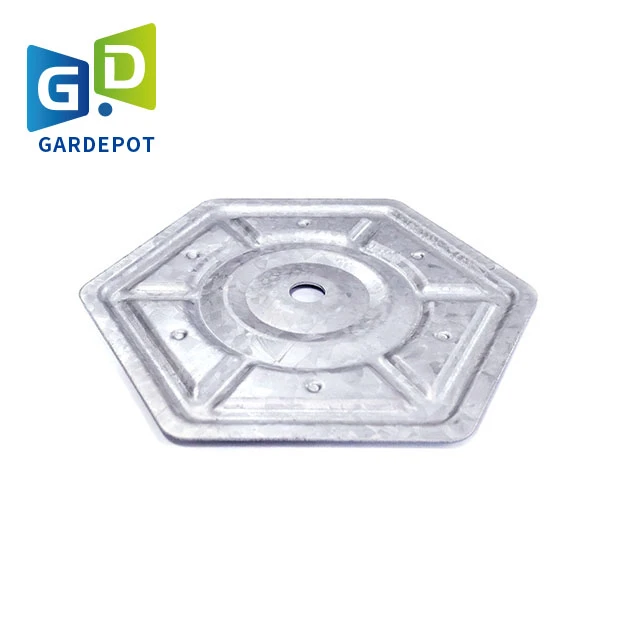
(1 8 black aluminum rivets)
FAQS on 1 8 black aluminum rivets
Q: What size are 1/8 black aluminum rivets commonly used for?
A: 1/8 black aluminum rivets are commonly used for light-duty applications. They are ideal for joining thin materials like metal sheets and plastic. The black finish provides a sleek, corrosion-resistant appearance.
Q: How do 3/16 black aluminum rivets differ from 1/8 ones?
A: 3/16 black aluminum rivets are larger in diameter than 1/8 rivets and provide a stronger hold. They are suitable for thicker materials or when higher shear strength is needed. Both sizes feature a black coating for aesthetics and protection.
Q: What are the benefits of using black aluminum rivets?
A: Black aluminum rivets offer corrosion resistance and a stylish finish for visible applications. They are lightweight and easy to install. The black color also helps them blend with darker surfaces.
Q: Can 1/8 black aluminum rivets be used outdoors?
A: Yes, 1/8 black aluminum rivets can be used outdoors due to their corrosion resistance. Aluminum resists rusting, and the black coating offers extra protection. They're suitable for various outdoor projects.
Q: Do black aluminum rivets require special tools for installation?
A: No special tools are needed; a standard blind rivet tool or rivet gun suffices. Choose the correct nosepiece size for your rivet diameter. This makes black aluminum rivets easy to install on most projects.