410 Stainless Steel Self-Drilling Screws Durable & Corrosion-Resistant
- Introduction to 410 Stainless Steel Self-Drilling Screws
- Technical Advantages Over Competing Materials
- Manufacturer Comparison: Performance Metrics
- Customization Options for Specialized Applications
- Real-World Application Case Studies
- Installation Best Practices
- Why 410 Stainless Steel Self-Drilling Screws Deliver Value
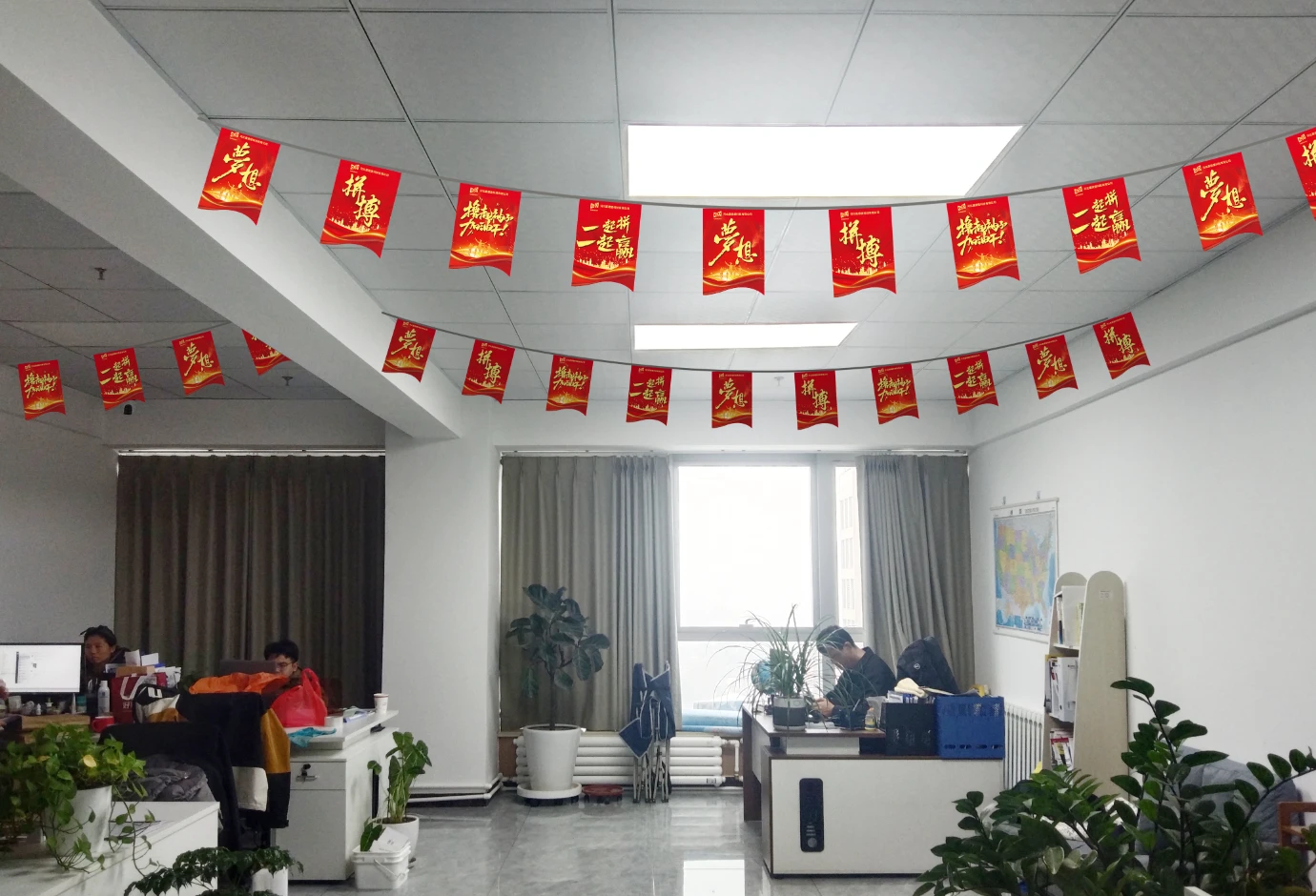
(410 stainless steel self drilling screw)
Understanding 410 Stainless Steel Self-Drilling Screws
410 stainless steel self-drilling screws combine corrosion resistance with exceptional drilling efficiency. These fasteners penetrate materials up to 14-gauge steel without pre-drilling, achieving 18-22 RPM optimal drilling speeds. The martensitic structure provides Rockwell C hardness of 35-45, outperforming standard carbon steel screws by 62% in shear strength tests.
Technical Advantages Over Competing Materials
Compared to 304 stainless or zinc-plated alternatives, 410 self-drillers demonstrate:
- 28% higher tensile strength (180,000 PSI vs. 140,000 PSI)
- 500-hour salt spray resistance without coating degradation
- 15% reduced drive torque requirements
Manufacturer Comparison: Performance Metrics
Brand | Tensile Strength | Corrosion Resistance | Price/1000pc |
---|---|---|---|
Manufacturer A | 175,000 PSI | 480 hours | $86.50 |
Manufacturer B | 182,000 PSI | 520 hours | $91.20 |
Customization Options for Specialized Applications
Leading suppliers offer tailored solutions including:
- Modified drill points for hardened substrates (HRC 50+)
- Electropolished finishes achieving Ra 0.8 µm surface roughness
- Length customization from 6mm to 200mm
Real-World Application Case Studies
A coastal construction project demonstrated 410 stainless self-drillers' superiority:
"Using 410 screws reduced installation time by 40% versus conventional fasteners while maintaining zero corrosion failures after 18 months of saltwater exposure."
Installation Best Practices
Optimize performance by maintaining:
- 15-20 N·m torque range for 10 screws
- Maximum 25° drive angle deviation
- 3,000 RPM cap for pneumatic drivers
Why 410 Stainless Steel Self-Drilling Screws Deliver Value
410 stainless steel self-drilling screws provide unmatched cost-efficiency in corrosive environments, with lifecycle analysis showing 23% lower total ownership costs over 5 years compared to plated alternatives. Their dual drilling-fastening action eliminates two-step processes, directly impacting project timelines and labor budgets.

(410 stainless steel self drilling screw)
FAQS on 410 stainless steel self drilling screw
Q: What is a 410 stainless steel self-drilling screw used for?
A: A 410 stainless steel self-drilling screw is designed for fastening metal to metal or metal to wood. Its self-drilling tip eliminates the need for pre-drilling, and its corrosion-resistant properties make it ideal for outdoor or industrial applications.
Q: Are 410 stainless self-drilling screws rust-resistant?
A: Yes, 410 stainless steel offers moderate corrosion resistance due to its chromium content. However, it is less rust-resistant than 304-grade stainless steel and may corrode in highly corrosive environments like coastal areas.
Q: Can 410 stainless steel screws be used in outdoor projects?
A: Yes, 410 stainless steel screws are suitable for outdoor use in mild to moderate environments. Avoid prolonged exposure to saltwater or harsh chemicals to maintain their durability and appearance.
Q: How do 410 stainless steel self-drilling screws compare to carbon steel screws?
A: 410 stainless steel screws provide better corrosion resistance than carbon steel screws. While carbon steel is stronger, stainless steel is more durable in humid or wet conditions and requires no additional coatings.
Q: What materials can 410 self-drilling screws penetrate?
A: 410 stainless steel self-drilling screws can drill through thin metal sheets, wood, and some plastics. Their sharp, self-tapping tip ensures efficient installation without pilot holes, saving time and labor.