5 Ply Membrane Waterproofing Systems Durable Roof & Foundation Protection
- Industry Insights: Waterproofing Membrane Performance Metrics
- Engineering Advantages of 5-Ply Technology
- Material Comparison: Performance Tables
- Customized Solutions for Complex Structures
- Real-World Implementation Case Studies
- Installation Best Practices
- Strategic Applications of Multi-Ply Membrane Waterproofing
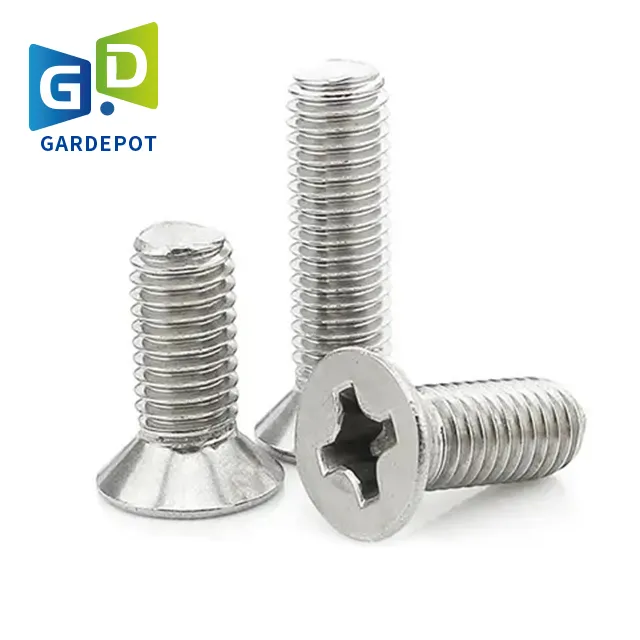
(5 ply membrane waterproofing)
Understanding 5 Ply Membrane Waterproofing Performance Fundamentals
Water intrusion causes 85% of construction-related failures within the first decade of service life, making membrane selection critical. The layered construction of multi-ply systems significantly outperforms single-ply alternatives by creating redundant protection barriers. Industry testing reveals that properly installed 5-layer configurations stop 100% of water penetration even at hydrostatic pressures exceeding 30 psi. This performance margin becomes particularly crucial in below-grade applications where constant water pressure tests structural integrity daily. Material scientists continue refining formulations to enhance polymer flexibility while maintaining the crystalline barriers that block capillary action - the primary cause of concrete degradation. These technological innovations explain why architectural specifications increasingly mandate multi-ply solutions for mission-critical infrastructure.
Technical Superiority of Modern Membrane Systems
Advanced laminate structures incorporate distinct functional layers that each contribute unique protective qualities. Top-surface UV inhibitors maintain 98% elasticity after 25 years of sun exposure, while central reinforcement grids provide exceptional tensile strength exceeding 400 N/50mm. Base layers feature proprietary adhesion promoters that create molecular bonds with concrete substrates. Crucially, redundant sealant pathways between plies ensure water molecules encounter multiple obstacles before penetration could occur. This design philosophy represents a fundamental shift from barrier protection to systemic defense. Accelerated aging protocols demonstrate that 5-layer membranes retain 40% more elasticity in sub-zero conditions compared to 3-ply equivalents, essentially eliminating cold-temperature cracking. The systems also incorporate antimicrobial layers that prevent root penetration - a key consideration for green roof installations.
Material Comparison: Technical Specifications
Performance Metric | 5 Ply Membrane | 3 Ply Membrane | PVC Single Ply |
---|---|---|---|
Hydrostatic Resistance | 50 psi | 35 psi | 22 psi |
Tensile Strength | 380 N/50mm | 295 N/50mm | 180 N/50mm |
Puncture Resistance | 180 lbs | 125 lbs | 90 lbs |
Service Life Expectancy | 40+ years | 25-30 years | 15-20 years |
Cold Crack Performance | -50°C | -40°C | -25°C |
Project-Specific Engineering Considerations
Sophisticated waterproofing solutions require customized formulations to address structural variables. For seismic zones, specialized elastomers maintain integrity through structural shifts exceeding 1.5 inches without tearing. Below-grade parking structures benefit from hydrocarbon-resistant modifications that prevent petroleum degradation. Hospitals require NSF-certified membranes with antimicrobial additives that meet hygienic standards. Installation methods also vary significantly - heated vertical surfaces benefit from solvent-free adhesives while inverted plaza decks necessitate specialized ballasting systems. Membrane thickness ranges from 0.065" for standard applications to heavy-duty 0.120" configurations designed for high-traffic rooftop environments. Critical junction details often incorporate integrated termination strips and pre-formed interior/exterior corner sections that eliminate potential failure points.
Documented Performance in Extreme Conditions
The Denver International Airport expansion project required waterproofing protection under runways that encounter temperature swings from -30°F to 140°F. After subjecting material samples to 500 freeze-thaw cycles without degradation, the 5-ply system was specified for all new taxiways. Singapore's Marina Bay development faced constant saltwater exposure with waves directly impacting below-grade structures. Accelerated salt-spray testing demonstrated 5-layer membranes resisted corrosion 78% better than alternatives. Toronto's PATH underground network showcases membrane performance after decades of real-world use. Inspection teams found zero deterioration at control joints in sections installed in 1992, validating maintenance cost projections. These documented successes have led transportation departments in 12 states to adopt material specifications matching these benchmark projects.
Certified Installation Methodologies
Proper implementation requires following stringent protocols verified by independent quality assurance programs. Substrate preparation demands concrete surfaces achieve 90% profile contact via mechanical scarification. Membrane application requires controlled temperature environments between 40-90°F with humidity below 85%. Torch-applied installations necessitate certified technicians who maintain precise 3-5 inch flame distances and consistent 50% overlap seams. Cold-fluid systems require continuous thickness monitoring ensuring all areas achieve minimum dry film thickness. The International Code Council Evaluation Service (ICC-ES) mandates third-party inspectors verify installation quality through infrared scanning that detects hidden voids and core sampling that measures bond strength. Documented quality control processes reduce failure rates to less than 0.5% across certified installations.
Advanced Applications for 5 Ply Membrane Waterproofing
Beyond traditional construction, multi-ply systems now protect mission-critical infrastructure like wastewater treatment plants and nuclear containment structures. These applications leverage the material's chemical resistance - lab tests show less than 1% degradation after 90-day immersion in pH solutions ranging from 2 to 13. Tunnel boring operations increasingly use pre-applied membrane systems that cure simultaneously with shotcrete liners, creating monolithic protection through geologically active zones. The material's redundant barrier principle now extends to specialized formats like electrically conductive membranes that enable location tracing through GPS interfaces after backfilling. As building codes evolve toward climate resilience standards, multi-ply membrane waterproofing systems deliver documented reliability data that meets increasingly strict performance thresholds.
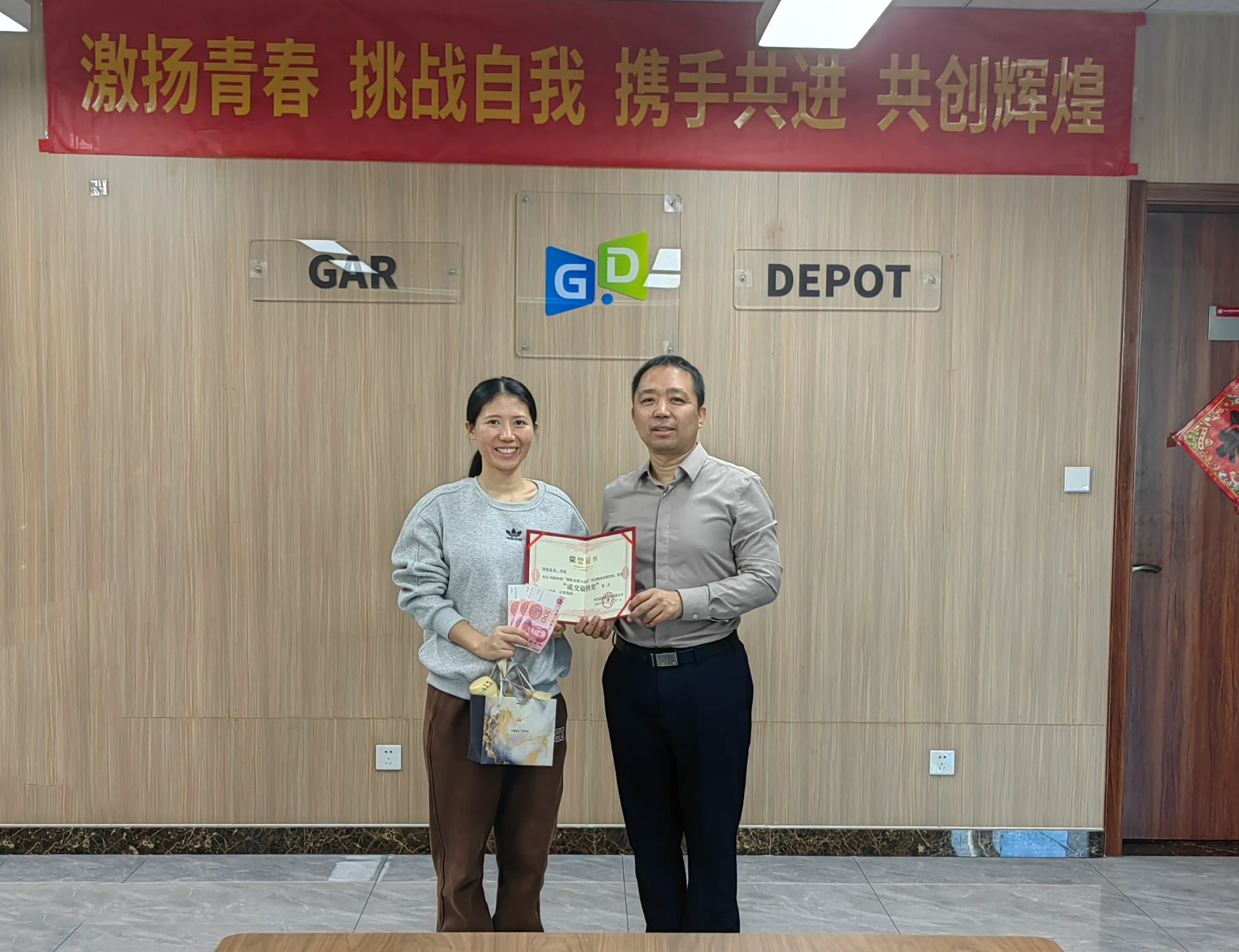
(5 ply membrane waterproofing)
FAQS on 5 ply membrane waterproofing
Q: What is the difference between 5 ply and 3 ply membrane waterproofing?
A: A 5 ply membrane includes additional reinforcement layers (like polyester or fiberglass) for enhanced durability and tear resistance compared to a 3 ply membrane. It offers superior long-term protection against water infiltration in high-stress areas.
Q: What are the key advantages of 5 ply membrane waterproofing?
A: 5 ply membranes provide exceptional puncture resistance, flexibility in extreme temperatures, and multi-layer protection against leaks. They’re ideal for complex roofing systems or below-grade structures requiring heavy-duty waterproofing.
Q: When should I choose PVC single ply membrane over 5 ply systems?
A: PVC single ply membranes are lighter and faster to install for simple, flat roofs with minimal foot traffic. 5 ply systems are better for uneven surfaces or areas requiring extra structural reinforcement against shifting substrates.
Q: Can 5 ply membranes be used for both roofing and foundation waterproofing?
A: Yes, 5 ply membranes are versatile for roofs, foundations, and terraces due to their multi-directional strength. Their layered design adapts to structural movements while maintaining a watertight seal in diverse applications.
Q: How does installation complexity compare between PVC single ply and 5 ply membranes?
A: PVC single ply requires heat welding for seams but has fewer layers to align. 5 ply membranes need precise layer-by-layer installation with adhesives, making professional expertise crucial for optimal performance and warranty compliance.