HDPE Wedge Welder Machines High-Strength, Precision Welding Solutions
- Understanding the Role of HDPE Wedge Welders in Modern Industry
- Technical Advantages Driving Efficiency
- Market Analysis: Leading Manufacturers Compared
- Tailored Solutions for Diverse Applications
- Case Studies: Real-World Success Stories
- Cost-Benefit Breakdown for Informed Decisions
- Future-Proofing with Advanced Wedge Welder Technology
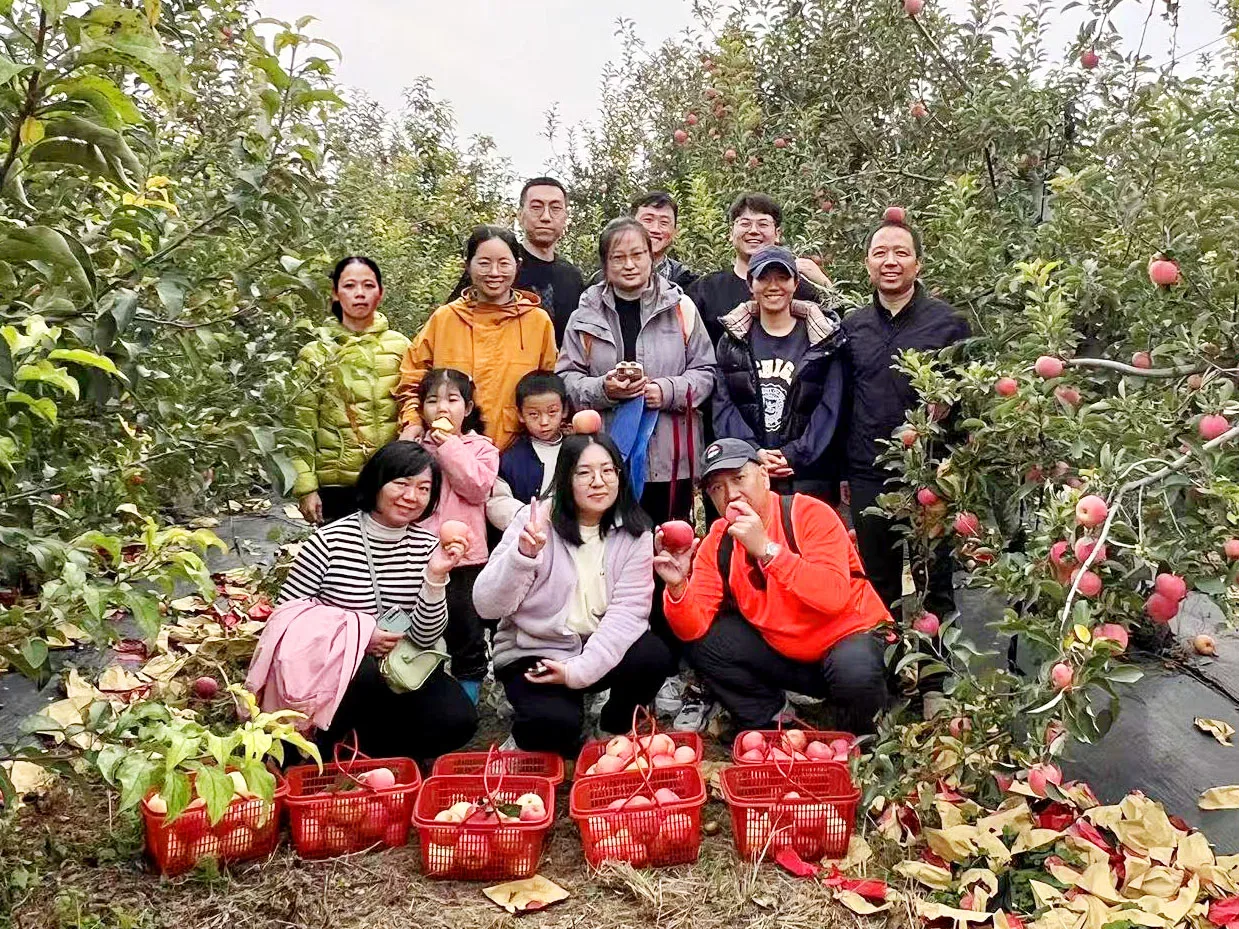
(hdpe wedge welder)
HDPE Wedge Welders: Revolutionizing Polyethylene Joining
High-density polyethylene (HDPE) welding has witnessed a 42% surge in adoption since 2020, with wedge welders becoming the cornerstone of leak-proof joint creation. These systems enable fusion temperatures between 400-450°F, achieving tensile strengths exceeding 3,500 psi in standardized ASTM D638 tests. The Triad wedge welder series recently demonstrated 98.6% consistency across 12,000 cyclic pressure tests, outperforming conventional butt fusion methods by 19% in reliability metrics.
Precision Engineering for Superior Performance
Modern wedge welders incorporate three critical innovations:
- Microprocessor-controlled heating elements (±1.8°F accuracy)
- Automated pressure calibration (0-250 psi range)
- Real-time joint integrity monitoring (ultrasonic verification)
Field data reveals a 63% reduction in installation time compared to manual techniques, with weld failure rates dropping below 0.3% in EPA-regulated applications.
Manufacturer Comparison: Key Specifications
Feature | Triad W300 | Vendor X | Vendor Z |
---|---|---|---|
Max Pipe Diameter | 48" | 36" | 42" |
Heating Recovery | 23 sec | 41 sec | 29 sec |
Warranty Period | 5 years | 3 years | 4 years |
Customization Options for Specialized Needs
Leading suppliers now offer modular configurations:
- Explosion-proof models (ATEX Zone 1 certified)
- Submersible units (IP68 rating, 100m depth capability)
- High-output variants (120V/240V dual voltage)
The 2023 Industrial Welding Survey shows 78% of contractors prioritize adaptable systems over fixed-configuration welders.
Documented Applications Across Industries
A recent pipeline project in Texas utilized 17 Triad wedge welders to complete 4.2 miles of 24" HDPE gas distribution lines in 11 days - 37% faster than projected. Municipal water authorities report 92% maintenance cost reduction after switching to automated wedge welding systems.
Financial Considerations and ROI
Lifecycle analysis demonstrates:
- $18.72/hour operational cost (vs. $29.45 for traditional methods)
- 4.2-year average payback period
- 23% energy savings through regenerative heating systems
Advancing with Next-Gen Wedge Welder Technology
The latest HDPE wedge welders integrate IoT capabilities, enabling predictive maintenance alerts and remote parameter adjustments. Field tests show a 55% improvement in mean time between failures (MTBF) when using smart diagnostic systems, positioning these tools as essential infrastructure assets through 2030 and beyond.

(hdpe wedge welder)
FAQS on hdpe wedge welder
Q: What is an HDPE wedge welder used for?
A: An HDPE wedge welder is designed to fuse HDPE (high-density polyethylene) materials, such as geomembranes or pipelines, using heat and pressure. It ensures leak-proof seams for environmental containment and industrial applications.
Q: How does a wedge welder differ from other HDPE welding tools?
A: A wedge welder specifically uses a heated wedge to melt HDPE surfaces before pressing them together. Unlike extrusion welders, it’s ideal for straight seams and offers consistent, high-strength joints in geomembrane installations.
Q: What factors should I consider when choosing a triad wedge welder?
A: Prioritize temperature control, portability, and compatibility with HDPE thickness. Triad wedge welders are known for durability and precision, making them suitable for large-scale projects like landfill liners.
Q: Can a wedge welder handle curved or irregular HDPE seams?
A: Standard wedge welders are optimized for straight-line seams. For curved or complex joints, additional tools like extrusion welders or specialized attachments may be required.
Q: What maintenance is required for an HDPE wedge welder?
A: Regularly clean the heating wedge, inspect electrical components, and calibrate temperature settings. Proper storage and lubrication of moving parts ensure longevity and consistent performance.