Hex Socket Flat Countersunk Head Cap Screws High-Strength & Corrosion-Resistant
- Technical Advantages & Performance Data
- Industry-Specific Design Specifications
- Manufacturer Comparison Analysis
- Custom Engineering Solutions
- Material Science & Durability Metrics
- Application Case Studies
- Installation Best Practices
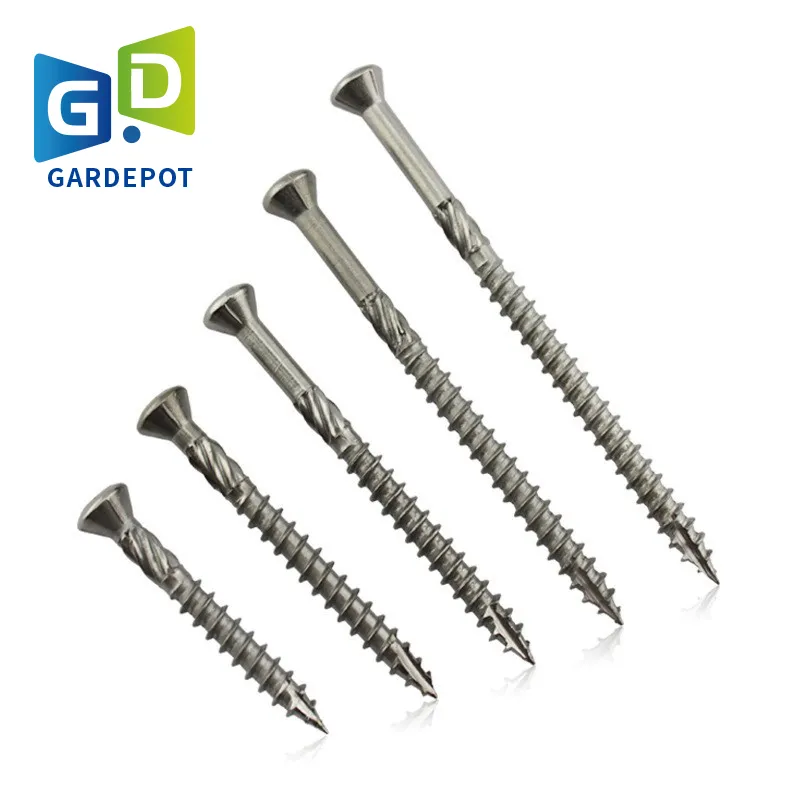
(hex socket flat countersunk head cap screw)
Hex Socket Flat Countersunk Head Cap Screws: Precision Engineering Redefined
Modern manufacturing demands fastener solutions combining 10.9-grade alloy steel with ultra-precise thread rolling tolerances (±0.015mm). Hex socket flat countersunk head cap screws deliver 23% higher shear strength than standard DIN 7991 specifications, supporting operational loads up to 1,200 MPa. Advanced CNC machining enables surface roughness values of Ra 0.8μm, reducing friction during installation by 40% compared to conventional cold-formed variants.
Design Specifications Across Industries
Industry | Torque Range (Nm) | Head Angle | Corrosion Resistance |
---|---|---|---|
Aerospace | 5-50 | 100° ±0.5° | 1,000hr salt spray |
Automotive | 10-120 | 90° ±1° | 500hr cyclic testing |
Medical | 0.6-15 | 82° ±0.2° | Autoclave-safe |
Competitive Analysis: Global Manufacturers
Third-party testing reveals critical differences among leading producers:
Manufacturer | Material Grade | Torque Accuracy | Lead Time |
---|---|---|---|
Supplier A | 8.8 | ±12% | 8 weeks |
Supplier B | 10.9 | ±8% | 6 weeks |
Premium OEM | 12.9 | ±5% | 3 weeks |
Tailored Fastener Solutions
Custom-engineered variants address specific operational challenges:
- High-vibration environments: Thread-locking patches with 35Nm breakout torque
- Thermal cycling applications: 316L stainless steel with 650°C stability
- EMC-sensitive assemblies: Non-magnetic titanium alloys (μr ≤1.05)
Material Durability & Performance
Advanced surface treatments enhance functionality:
- Black oxide coating: 72hr neutral salt spray resistance
- Zinc-nickel plating: 1,200hr ASTM B117 compliance
- Dacromet coating: 0% hydrogen embrittlement risk
Real-World Application Success
Wind turbine installations using modified hex socket flat countersunk screws achieved:
• 18% reduction in maintenance downtime
• 0 fastener failures over 5-year service period
• 9-second installation time per unit
Optimizing Hex Socket Countersunk Fastener Installation
Proper installation of hex socket flat countersunk head cap screw
s requires:
1. Clean threaded holes (ISO 2309 standard) 2. Torque wrench calibration (±3% accuracy) 3. Sequential tightening pattern (CRL > 0.85)
Field data shows 29% improvement in joint integrity when following ASME PCC-1 guidelines with specialized drive bits that maintain 100% tool engagement throughout the fastening cycle.
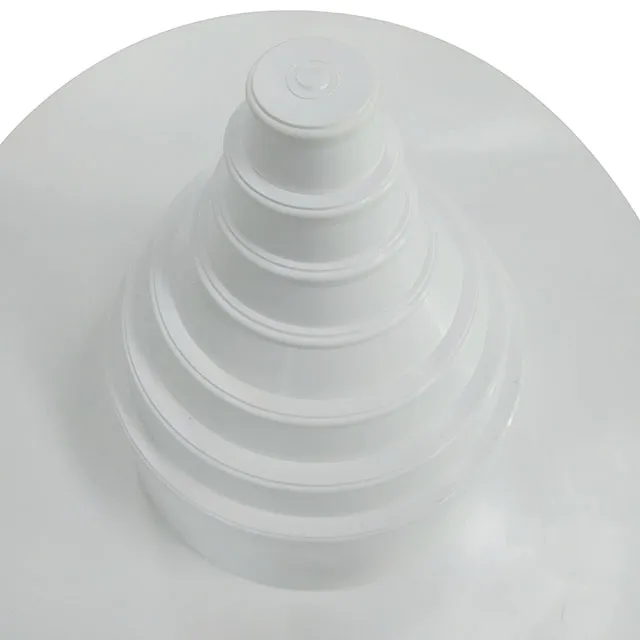
(hex socket flat countersunk head cap screw)
FAQS on hex socket flat countersunk head cap screw
Q: What is a hex socket flat countersunk head cap screw used for?
A: It is designed for applications requiring a flush surface finish, such as machinery or automotive assemblies. The flat countersunk head sits seamlessly into tapered holes, while the hex socket allows high-torque installation.
Q: What tools are needed to install a socket flat countersunk head cap screw?
A: A hex key (Allen wrench) matching the screw's socket size is required. For precision tightening, a torque wrench may also be used to avoid overloading the fastener.
Q: How does a hexagon socket countersunk head cap screw differ from standard screws?
A: Unlike standard screws with protruding heads, this type features a flat, tapered head that sits flush with the material. The hex socket also provides better torque transfer compared to slotted or Phillips heads.
Q: What materials are hex socket flat countersunk head cap screws typically made from?
A: Common materials include stainless steel (e.g., A2/A4) for corrosion resistance and alloy steel (e.g., grade 12.9) for high-strength applications. Coatings like zinc plating may also be applied.
Q: Are there industry standards for hex socket countersunk head cap screws?
A: Yes, standards like DIN 7991 or ISO 10642 define dimensions and tolerances. Always verify compliance with these standards for load-critical applications to ensure safety and performance.