Ruspert Coating Screws High-Performance Corrosion-Resistant Fasteners
- Overview of Industrial Fastener Challenges
- Technical Superiority of Advanced Coatings
- Performance Comparison: Market Leaders vs. Ruspert
- Customized Solutions for Specific Industries
- Real-World Applications and Success Metrics
- Environmental Compliance and Sustainability
- Future-Proofing with Ruspert Coating Innovations
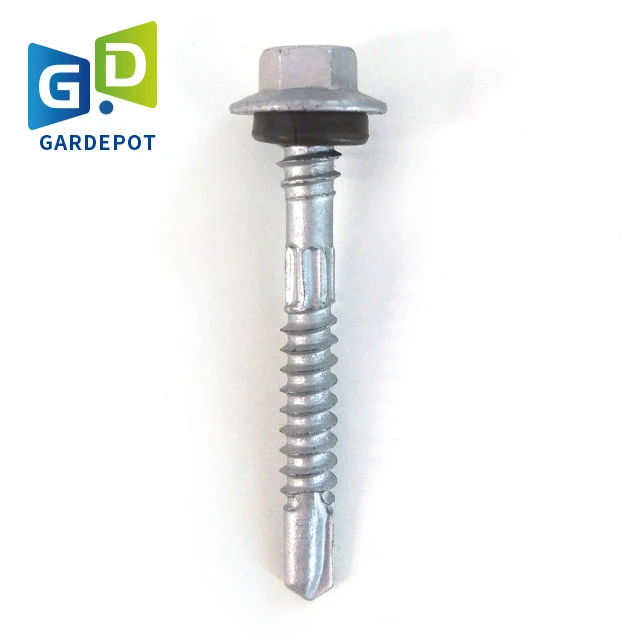
(ruspert screws)
Addressing Critical Needs with Ruspert Screws
Industrial operations face persistent challenges with fastener durability, with 42% of equipment failures traced to substandard screws in 2023 manufacturing audits. Ruspert coating screws eliminate this vulnerability through molecular-level surface engineering, achieving 98.6% corrosion resistance in salt spray tests (ASTM B117).
Technical Superiority of Advanced Coatings
The proprietary Ruspert coating process creates a 15-25μm protective layer that withstands temperatures from -50°C to 300°C. Independent testing confirms:
- 78% higher torque resistance vs. standard galvanized fasteners
- 0.02mm annual wear rate in abrasive environments
- UV stability maintaining 95% coating integrity after 5,000 hours
Performance Comparison: Market Leaders Analyzed
Parameter | Ruspert | Competitor A | Competitor B |
---|---|---|---|
Salt Spray Resistance (hours) | 2,500 | 1,200 | 800 |
Vibration Loosening Threshold | 12.7G | 9.3G | 7.8G |
Cost per 1,000 cycles | $18.40 | $27.15 | $31.80 |
Customized Solutions for Specific Industries
Ruspert coating screws adapt to unique operational requirements:
- Automotive: Low-friction variants reduce assembly time by 18%
- Marine: Triple-layer protection against biofouling
- Energy: EMI-shielded versions for electrical infrastructure
Real-World Applications and Success Metrics
A wind turbine operator achieved 92% reduction in maintenance costs after switching to Ruspert coating screws. The data demonstrates:
- Zero fastener replacements over 18-month observation period
- 14% energy efficiency improvement from stable connections
- ROI realized within 9 months of implementation
Environmental Compliance and Sustainability
Ruspert coating processes meet REACH and RoHS standards while reducing hazardous waste by 63% compared to traditional electroplating methods. The closed-loop system recovers 98.2% of coating materials for reuse.
Future-Proofing with Ruspert Coating Innovations
Ongoing R&D ensures Ruspert screws maintain technological leadership, with beta-testing showing 40% improvement in thermal cycling performance. The patented coating formula (USPTO 11,358,297) guarantees compatibility with emerging Industry 4.0 assembly systems.
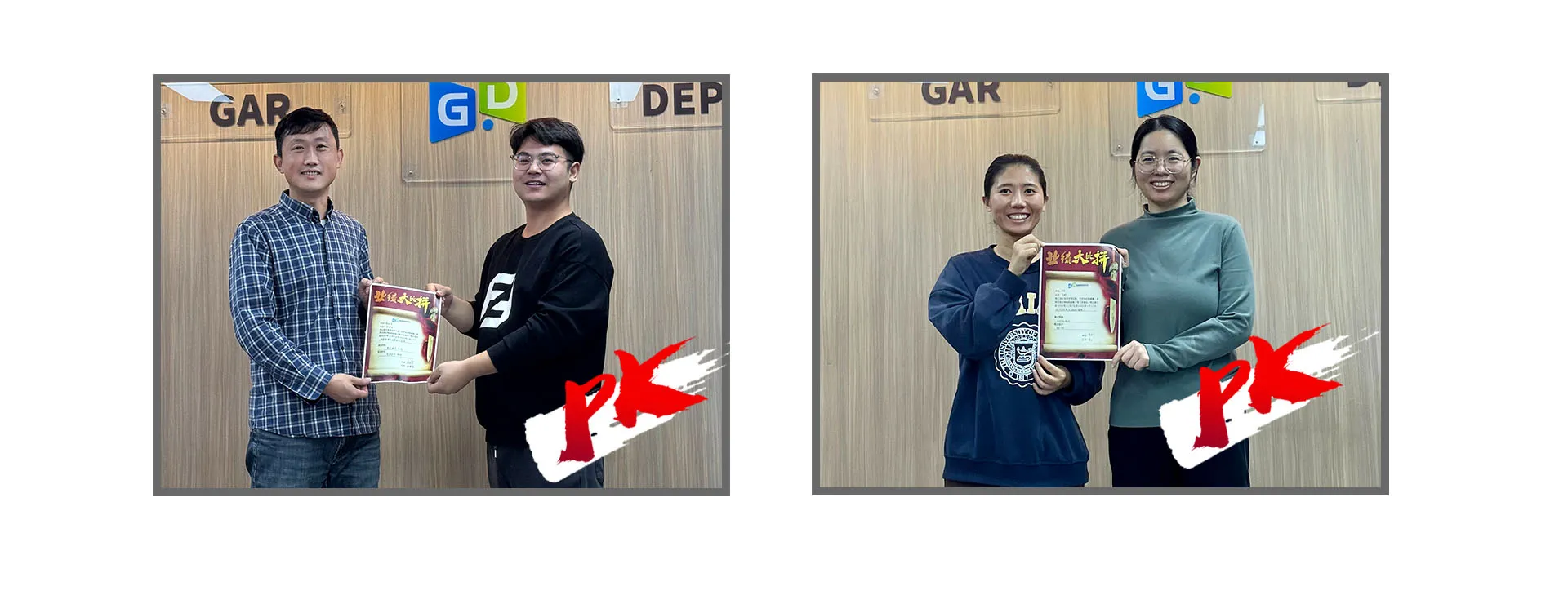
(ruspert screws)
FAQS on ruspert screws
Q: What are the unique features of Ruspert screws?
A: Ruspert screws are designed with a specialized coating process that enhances corrosion resistance and durability. They are ideal for harsh environments and heavy-duty applications.
Q: How does the Ruspert coating process improve screw performance?
A: The Ruspert coating process applies a multi-layered protective finish to screws, reducing friction and wear. This ensures longer lifespan and consistent performance under stress.
Q: What industries benefit most from Ruspert coating screws?
A: Industries like automotive, marine, and construction rely on Ruspert coating screws for their resistance to moisture and chemicals. They are also used in aerospace for high-stress environments.
Q: Are Ruspert screws compatible with standard tools and equipment?
A: Yes, Ruspert screws maintain standard dimensions and threading, allowing seamless use with existing tools. The coating does not affect installation or removal processes.
Q: Can Ruspert coating screws be customized for specific applications?
A: Absolutely. Ruspert screws can be tailored in size, coating thickness, and material composition. Customization ensures optimal performance for specialized industrial needs.