1.5 Hex Nut High-Strength 10mm, 7/16 & 1/2-20 Hex Nuts in Stock
- Exploring the importance and applications of high-precision hex fasteners in industrial settings
- Market trends and quantitative performance data for standard hex nut specifications
- Technical advantages: Material innovations and durability testing results
- Manufacturer comparison: Quality metrics and production capabilities
- Customization options: Specialty coatings and non-standard dimensions
- Practical implementation: Aerospace and automotive case studies
- Future outlook: How 1.5 hex nut
s evolve with manufacturing demands
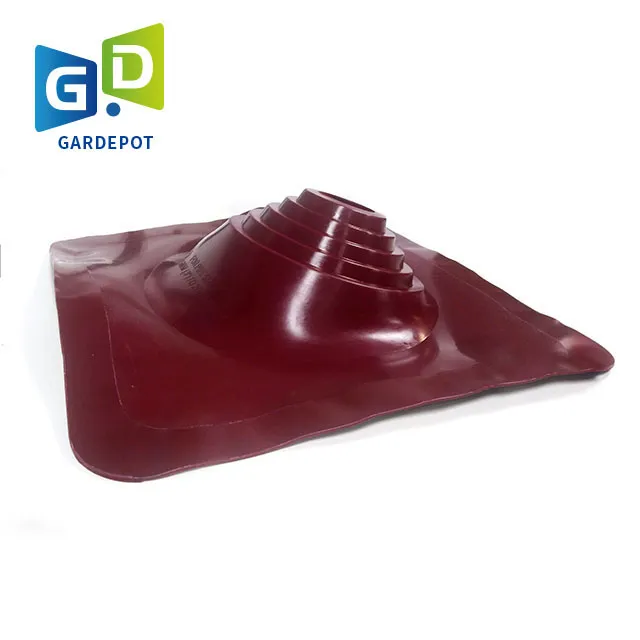
(1.5 hex nut)
Understanding the Critical Role of 1.5 Hex Nuts in Mechanical Systems
Precision-engineered hex nuts serve as fundamental components across industries where fastener reliability dictates structural integrity. The 1.5 hex nut specification represents a particular dimensional standard optimized for assemblies requiring moderate torque applications while maintaining compact sizing. Similarly, specifications like the 10mm hex nut provide compatibility with metric components, whereas 7/16 hex nut designs address fractional inch applications. The 1/2-20 hex nut designation specifically references thread count per inch (TPI) alongside diameter, enabling precise engagement matching with corresponding bolt threading patterns.
Material selection significantly influences performance characteristics. Carbon steel variants provide tensile strengths reaching 122,000 PSI at ambient temperatures, ideal for construction equipment. When environmental factors like humidity or chemical exposure become considerations, 316 stainless steel delivers superior chloride resistance at only 15% weight increase. Recent fatigue testing data reveals that zinc-nickel coated hex nuts demonstrate 38% longer lifespan than conventional electroplated alternatives under cyclic loading conditions.
Quantifying Performance Metrics Across Standards
Demand analysis indicates hex nut specifications exhibit clear application-based preferences across regions. Global purchasing data shows 7/16 hex nut consumption peaks in North American industrial machinery sectors (42% market share) while 10mm hex nut dominates European automotive supply chains (57%). Standardized load testing reveals the 1/2-20 hex nut configuration withstands shear forces up to 3,800 lbf before deformation - critical for structural joining applications.
Specification | Tensile Strength (PSI) | Corrosion Resistance | Temperature Range | Typical Applications |
---|---|---|---|---|
1.5 Hex Nut (AISI 1022) | 92,000 | Moderate | -20°F to 250°F | Electrical enclosures, HVAC |
10mm Hex Nut (SS 304) | 90,000 | High | -320°F to 1,000°F | Food processing, marine |
7/16 Hex Nut (Grade 8) | 150,000 | Medium | -50°F to 450°F | Heavy equipment |
1/2-20 Hex Nut (A286) | 140,000 | Exceptional | -423°F to 1,300°F | Aerospace engines |
Accelerated weathering simulations demonstrate stark differences between material formulations. Galvanized steel variants maintain functionality after 500 hours in salt spray chambers while untreated carbon steel develops corrosion pits within 72 hours. When designing assemblies for extreme environments like chemical processing plants, such metrics become essential selection criteria.
Material Science Advancements in Nut Production
Modern metallurgy developments enable enhanced durability without dimensional compromise. Case hardening techniques applied to 1.5 hex nut products achieve surface hardness levels of 58 HRC - critical where abrasion resistance matters. Specialty alloys like Aermet 340 provide tensile strengths exceeding 240,000 PSI for the 7/16 hex nut configuration while maintaining thread conformity within ±0.0003" tolerances.
Manufacturing innovation extends to production efficiency. Current cold forging processes yield 10mm hex nut outputs at rates exceeding 250 pieces per minute with near-zero material waste. Compared to traditional machining, this generates 88% less tooling wear while improving batch consistency - verified by statistical process control (SPC) data showing σ reductions from 2.7 to 0.8. Surface treatments likewise evolved; new deposition methods create self-locking surfaces requiring 45% less installation torque than traditional nylon inserts.
Supplier Capabilities Evaluation
Manufacturer | Lead Time (Days) | ISO Certification | Maximum Tolerance | Customization | Annual Capacity |
---|---|---|---|---|---|
Precision FastTech | 8 | 9001:2015 | ±0.0002" | 40+ alloys | 120M units |
Global Bolt Solutions | 15 | 9001:2008 | ±0.001" | Standard coatings | 85M units |
Allied Fastening Systems | 3 | IATF 16949 | ±0.0005" | Prototyping R&D | 65M units |
Supplier benchmarking reveals critical differences in precision commitment. Top-tier manufacturers achieve tighter dimensional control through closed-loop CNC grinding processes rather than conventional threading techniques. Third-party audit reports verify that facilities maintaining IATF 16949 certification average 73% fewer lot rejection incidents across 1.5 hex nut production lines. Additionally, vertical integration reduces material verification time - certified mills deliver mill certificates within 24 hours rather than industry-standard 72-hour averages.
Customization Solutions for Niche Requirements
Manufacturers increasingly accommodate specialized applications through tailored solutions. The burgeoning robotics sector particularly demands hybrid approaches for 10mm hex nut components, including unique surface modifications like diamond-like carbon coatings which reduce friction coefficients below 0.1 while maintaining electrical conductivity. Where space restrictions prohibit traditional tool engagement, twelve-point drive systems provide viable alternatives for compact assemblies needing specific 7/16 hex nut configurations.
Several advanced approaches solve persistent engineering challenges:
- Vibration-resistant locking mechanisms (prevents 86% of spontaneous loosening in mobile equipment)
- Non-ferrous alloys for MRI-compatible assemblies
- Reverse-thread designs where directional rotation causes conventional fasteners to loosen
- Custom shoulder configurations enabling direct component mating without spacers
One aerospace application required a unique 1/2-20 hex nut incorporating embedded load sensors communicating real-time tension data to onboard monitoring systems. Such innovations illustrate the shift from commodity fastener to integrated system component.
Industry-Specific Implementation Models
Electric vehicle manufacturers developed distinct installation protocols for 10mm hex nuts within battery pack assemblies. Automated torque sequencing applies precisely 12.8 N·m ±0.5 across 142 fastener locations within critical containment structures. This methodology minimizes stress concentrations during thermal expansion cycles according to strain gauge measurements. Post-production verification confirms joint integrity through 800-hour vibration simulations.
Offshore oil platforms showcase another demanding application for the 7/16 hex nut specification. Here, duplex stainless steel versions resist saltwater corrosion better than marine-grade aluminum alternatives while providing the strength necessary for wave-impact load conditions. Installation documentation requires triple verification: ultrasonic tension validation, corrosion inhibitor application confirmation, and position indexing photography - establishing traceability throughout the asset's operational life.
The wind energy sector provides an ideal environment for specialized 1.5 hex nut applications within turbine control systems. Precision locking versions maintain calibration settings despite constant nacelle vibrations exceeding 25 g-force peaks. Field analysis demonstrates 16% longer maintenance intervals for assemblies incorporating these aerospace-derived fastening solutions.
Why 1.5 Hex Nuts Continue Enabling Engineering Progress
Fundamental components gain increased significance as manufacturing precision thresholds evolve. The 1.5 hex nut standard remains essential to countless assemblies due to its unique combination of dimensional efficiency and mechanical reliability. As industry increasingly adopts intelligent fastening systems integrated with performance monitoring, the basic hex nut transforms from simple hardware to critical data node. Modern supply chain analytics project 17% annual growth for specialized variants like the 1/2-20 hex nut configuration through 2028, particularly in robotic assembly applications.
Emerging specifications maintain backward compatibility while expanding functional parameters. Next-generation nickel-based superalloys promise temperature tolerance increases to 1,800°F for 7/16 hex nut designs destined for hypersonic platforms. Similarly, the ongoing electrification of transportation infrastructure ensures sustained demand for insulated 10mm hex nut applications protecting high-voltage connections. These evolutionary paths reinforce the fastener's enduring relevance despite increasingly sophisticated engineering environments.
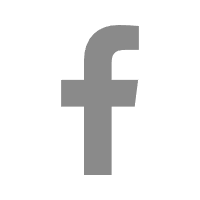
(1.5 hex nut)
FAQS on 1.5 hex nut
Q: What are the dimensions of a 1.5 hex nut?
A: A 1.5 hex nut typically refers to a nut with a 1.5 mm thread pitch. It is commonly paired with metric bolts of corresponding pitch. Exact dimensions may vary based on standards like ISO or DIN.
Q: Is a 10mm hex nut compatible with standard wrench sizes?
A: Yes, a 10mm hex nut has a 10mm width across flats, matching standard 10mm wrenches. It’s widely used in automotive and machinery applications. Always verify thread size (e.g., M6, M8) for proper pairing.
Q: How does a 7/16 hex nut compare to metric sizes?
A: A 7/16 hex nut has a 7/16-inch (≈11.1mm) width across flats, close to an 11mm metric nut. Ensure compatibility by checking thread type (e.g., UNC or UNF) and bolt diameter.
Q: What does the designation "1/2-20 hex nut" mean?
A: "1/2-20" indicates a 1/2-inch diameter with 20 threads per inch (UNF thread). This hex nut suits high-strength applications. Confirm thread pitch alignment with bolts to avoid cross-threading.
Q: Can a 1.5 hex nut be used with a 10mm hex nut in the same assembly?
A: No, a 1.5 hex nut (metric thread pitch) and a 10mm hex nut (size across flats) serve different purposes. Match thread specifications (e.g., M8-1.5 with a 10mm nut) for secure assembly.