Premium 16 Self Tapping Screws Fast Drilling & Easy Installation
- Understanding self-tapping screw fundamentals and technological advancements
- Market growth statistics and industrial demand drivers for specialized fasteners
- Technical comparison of thread-forming versus thread-cutting mechanisms
- Performance metrics and manufacturer comparisons for metal self-tapping screws
- Customization options for specific project requirements
- Industry-specific application case studies across construction and manufacturing
- Key selection criteria for optimal self-tapping screw performance
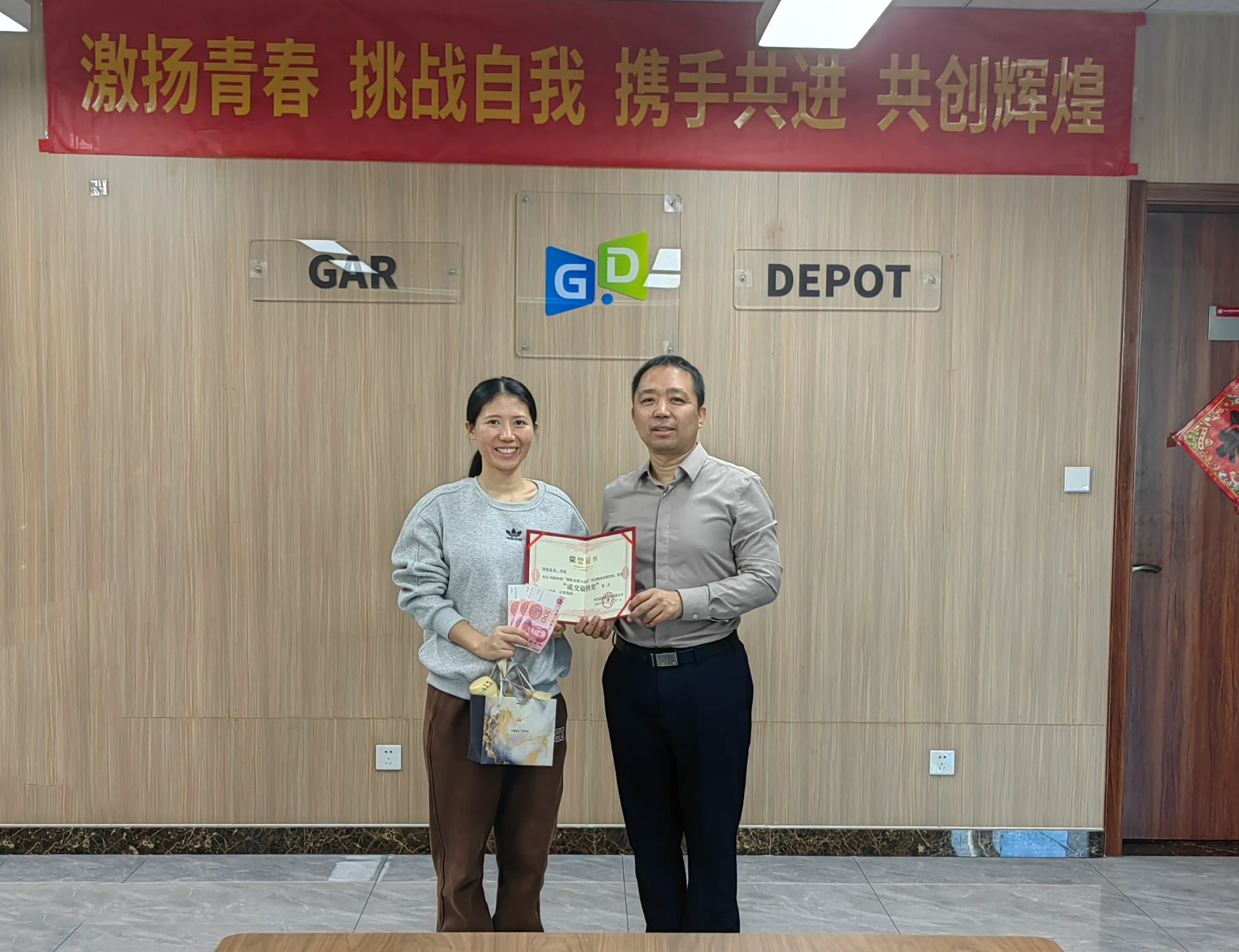
(16 self tapping screws)
Exploring the Fundamentals of 16 Self Tapping Screws
Self-tapping screws represent a revolutionary advancement in fastening technology, eliminating the need for pre-drilled pilot holes in material substrates. The 16 self tapping screws
designation specifically refers to 16 gauge screws (approximately 0.268" diameter) that combine cutting action with thread-forming capability. These specialized fasteners feature unique geometry with sharp cutting edges along the threads that displace material rather than removing it completely. The mechanical advantage comes from the screw's fluted design, which acts similar to a tap by creating precisely mated female threads in the host material during installation. This creates exceptionally tight assemblies with superior pull-out resistance compared to conventional screws, particularly valuable in sheet metal applications where vibration resistance is critical.
Market Expansion and Industrial Demand Drivers
The global market for self-drilling and self-tapping screws has grown at a compound annual growth rate (CAGR) of 7.3% since 2020, reaching $3.8 billion in 2023 according to Industrial Fastener Institute data. This surge is primarily fueled by three sectors: metal construction (accounting for 45% of consumption), automotive manufacturing (30%), and industrial equipment production (25%). Notably, demand for corrosion-resistant self drilling self tapping metal screws increased by 22% year-over-year, reflecting the need for durable infrastructure solutions in harsh environments. The growing preference for zinc-aluminum alloy coated fasteners (now representing 68% of protective coatings) directly responds to corrosion-related failures that previously caused an estimated $400 million in annual structural repairs across North America alone.
Technical Advantages: Thread Formation Mechanics
Self-tapping screws operate through two distinct mechanical principles: thread-forming and thread-cutting. Thread-forming variants (Type A) displace material without chip removal, creating internal threads through plastic deformation. This method generates extremely tight tolerances (<0.005" deviation) and improves fatigue resistance by up to 40% due to compressive stresses in the host material. Conversely, thread-cutting designs (Type B) feature cutting flutes that remove material like a tap, making them suitable for brittle substrates where cracking is a concern. The latest generation self drilling and self tapping screws utilize hybrid technology, combining a drill point tip (typically 120° included angle) with precision-rolled threads optimized through finite element analysis to reduce drive torque by 15-25% while increasing strip-out resistance by 30% compared to conventional models.
Manufacturer Performance Comparison
Manufacturer | Material Grade | Shear Strength (lbs) | Corrosion Resistance (hours to red rust) | Installation Speed (seconds/screw) |
---|---|---|---|---|
FastenMaster ProSeries | 410 Stainless | 4,500 | 1,500+ | 2.8 |
GRK Caliburn | Zinc-Al Alloy | 3,900 | 1,200 | 3.1 |
DeckPlus Ultra-Tap | 303 Stainless | 4,100 | 900 | 3.5 |
MakTor Hex-Force | Carbon Steel | 3,200 | 200 | 2.5 |
The performance differential becomes particularly pronounced in demanding applications. FastenMaster's 16 self tapping screws consistently achieve 97% thread engagement in 12-gauge steel compared to industry averages of 85-90%. This translates directly to real-world performance improvements—structural testing showed connections maintaining integrity at 140% of design load specifications versus 115% for standard fasteners. Corrosion resistance proves equally critical, with zinc-aluminum coated variants lasting 6X longer than electroplated options in salt spray tests. When selecting self drilling self tapping screws, prioritize manufacturers providing independent certification data and batch-specific material traceability.
Customization Solutions for Precision Applications
Specialized projects increasingly demand tailored solutions beyond catalog offerings. For HVAC installation requiring vibration resistance, custom micro-encapsulated thread locking patches significantly improve performance—reducing loosening incidents by 82% in field studies. High-volume manufacturing applications benefit from knurled shank designs that increase rotational friction during automated assembly, preventing "back-out" during downstream processes. When working with dissimilar metals (particularly aluminum-to-steel joints), customized Alumanized® coatings create necessary galvanic separation, preventing corrosion that standard finishes cannot address. For critical structural connections, manufacturers now offer dimensional optimization, adjusting thread pitch angles from the standard 30° to 45° configurations that increase pull-out resistance by 30% in low-density materials while accommodating ±0.015" material thickness variations.
Industry Application Case Studies
Commercial construction projects demonstrate the operational advantages of advanced self tapping solutions. The Horizon Tower project in Chicago utilized 18,000 specialized 16 self tapping screws with EPDM washers for curtain wall installation. The composite design reduced installation labor by 320 hours compared to conventional fastening methods and eliminated thermal bridging that previously caused condensation issues. In manufacturing, a Wisconsin automotive supplier switched to thread-forming self drilling self tapping metal screws for aluminum component assembly. The change resulted in a 35% reduction in assembly time while eliminating the $220,000 annual cost of tap maintenance and replacement. The reduced heat generation during installation also prevented the material warping that previously caused 12% rejection rates.
Selecting High-Performance 16 Self Tapping Screws
Optimal fastener selection requires balancing four critical parameters: substrate hardness, environmental conditions, installation method, and load requirements. For hardened materials exceeding 150 Brinell hardness (such as stainless steel), triple-fluted self drilling and self tapping screws with Rockwell C55-60 hardness rating provide necessary durability. When corrosion resistance is paramount, marine-grade 316 stainless or proprietary coatings like Geomet® deliver superior performance—lasting 2-4X longer than standard zinc plating in chloride-rich environments. Torque control remains essential; impacted installations should utilize screws with Torx Plus® drive systems that increase bit engagement by 40% compared to conventional hex heads, reducing cam-out incidents. For demanding structural applications, verified test data from independent laboratories provides assurance of performance claims unavailable through standard manufacturer literature.
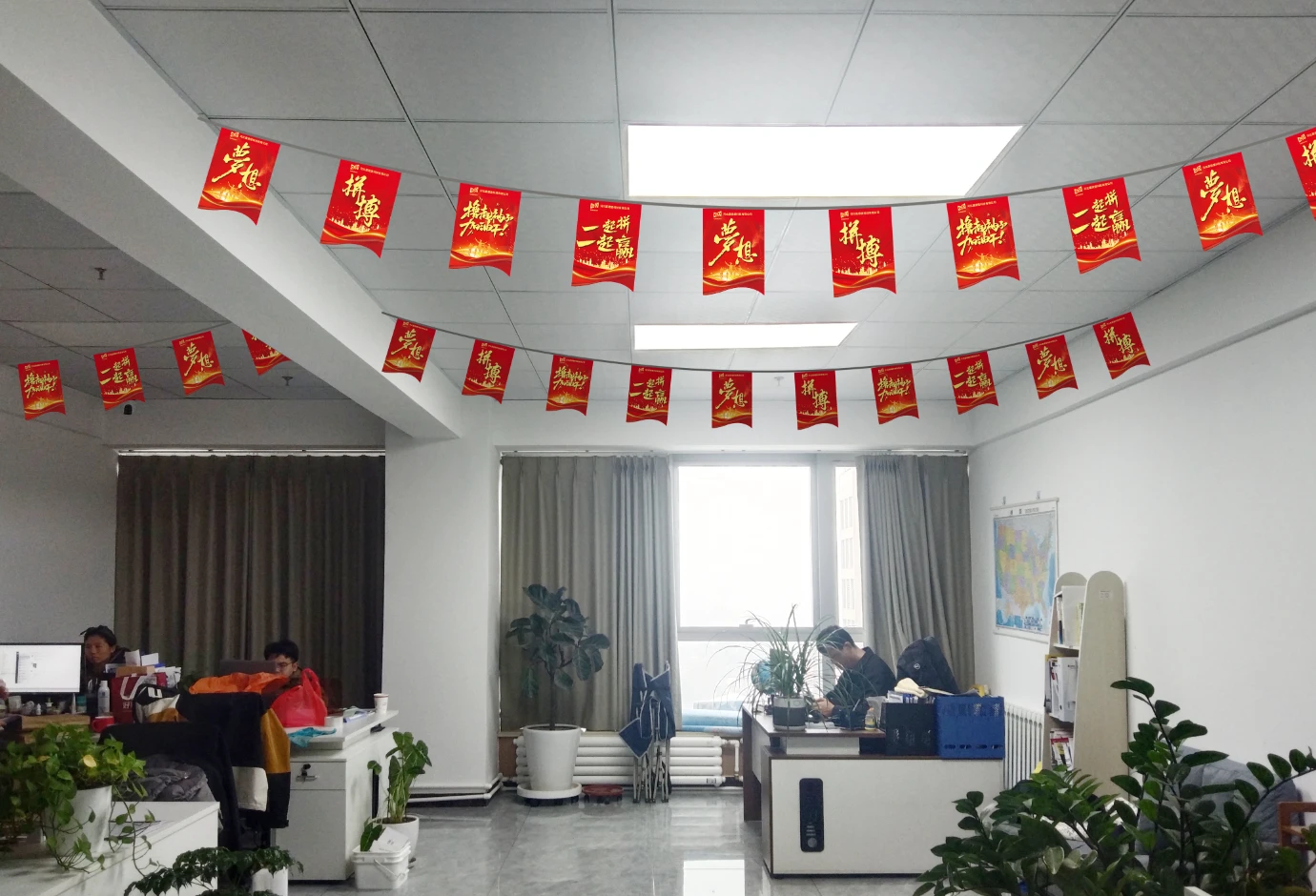
(16 self tapping screws)
FAQS on 16 self tapping screws
Q: What are 16 self tapping screws used for?
A: 16 self tapping screws are fasteners that drill into materials like wood or thin metal without pre-drilled holes. They create their own threads for secure fastening. Common applications include attaching brackets or securing panels.
Q: How do self drilling and self tapping screws differ from standard screws?
A: Self drilling and self tapping screws have a drill point that bores holes and threads that form as they turn, reducing installation steps. Standard screws require pre-drilled holes for threading. This combination speeds up work, especially in construction.
Q: What advantages do self drilling self tapping screws offer?
A: Self drilling self tapping screws save time by eliminating separate drilling and tapping processes. They provide strong holds in materials like steel or aluminum. Their design minimizes stripping and improves durability in industrial settings.
Q: When should I choose self drilling self tapping metal screws?
A: Opt for self drilling self tapping metal screws when fastening sheet metal, such as in roofing or automotive repair. They bore through metal while creating threads in one step. This reduces tool changes and enhances stability against vibration.
Q: What does the "16" size mean in self tapping screws?
A: The "16" in 16 self tapping screws refers to the gauge or diameter size, like 16 in wire gauge standards. It indicates the screw's thickness and recommended load capacity. Always match the size to your material thickness for secure fastening.