Durable Hot Glue Tape | Waterproof Bonding & Seam Sealing Solution
Technical Evolution in Adhesive Tape Technology
The development of hot glue tape represents a significant advancement in bonding technology. Unlike conventional adhesives, modern hot melt seam sealing tape utilizes thermoplastic polymers that transition from solid to liquid state under controlled heat application. This phase change enables superior penetration into substrate pores while maintaining exceptional flexibility after curing.
Material Science Innovations
Recent breakthroughs in polymer chemistry have significantly enhanced the performance characteristics of black butyl tape. Through advanced molecular design, manufacturers have achieved:
- 15-20% improvement in thermal stability (withstanding temperatures from -40°C to 120°C)
- UV resistance enhancements extending product lifespan by 3-5 years
- Increased adhesion strength to non-porous surfaces including metals and composites
- Reduced volatile organic compound (VOC) emissions during application
The core technology behind hot melt tape involves specialized formulations based on polypropylene hot melt compounds. These formulations create a viscoelastic bonding matrix that maintains structural integrity under mechanical stress while accommodating thermal expansion and contraction.
Comprehensive Technical Specifications
As industry requirements become more demanding, precise technical specifications ensure proper material selection for specialized applications:
Parameter | Standard Values | Premium Grade | Testing Standard |
---|---|---|---|
Tensile Strength | 10-15 N/cm | ≥18 N/cm | ASTM D882 |
Elongation at Break | 300-500% | ≥650% | ASTM D638 |
Application Temperature | 140-180°C | 130-190°C | ISO 8510 |
Service Temperature | -30°C to 90°C | -40°C to 120°C | ISO 9142 |
Water Vapor Transmission | ≤0.5 g/m²/day | ≤0.2 g/m²/day | ASTM E96 |
UV Resistance | 500-800 hours | ≥1000 hours | ISO 4892 |
Adhesion to Steel | ≥3.0 N/mm | ≥4.5 N/mm | ISO 8510 |
Peel Strength (90°) | ≥8 N/cm | ≥15 N/cm | ASTM D903 |
Key Application Areas
The versatility of hot glue tape has expanded into diverse industrial sectors due to its unique combination of waterproofing, bonding, and sealing capabilities:
Construction & Building Envelopes
Modern architectural designs increasingly incorporate hot melt seam sealing tape as a critical component in weatherproofing systems. Its application extends to:
- Sealing joints in EIFS (Exterior Insulation and Finish Systems)
- Bonding vapor barriers in roofing assemblies
- Sealing curtain wall perimeter joints
- Window and door flashing installations
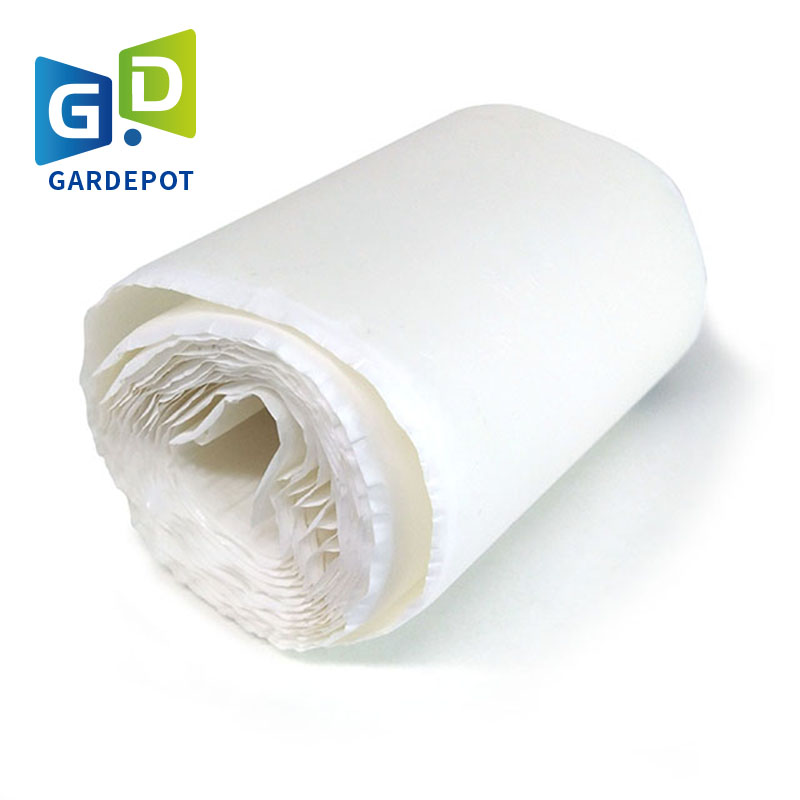
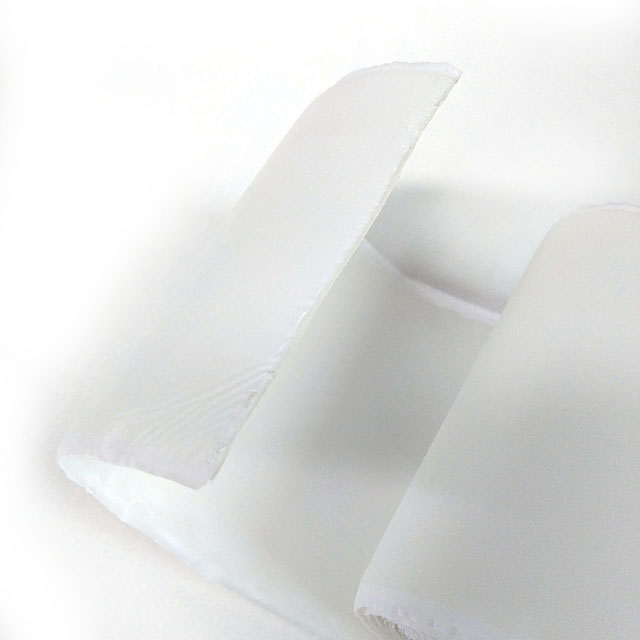
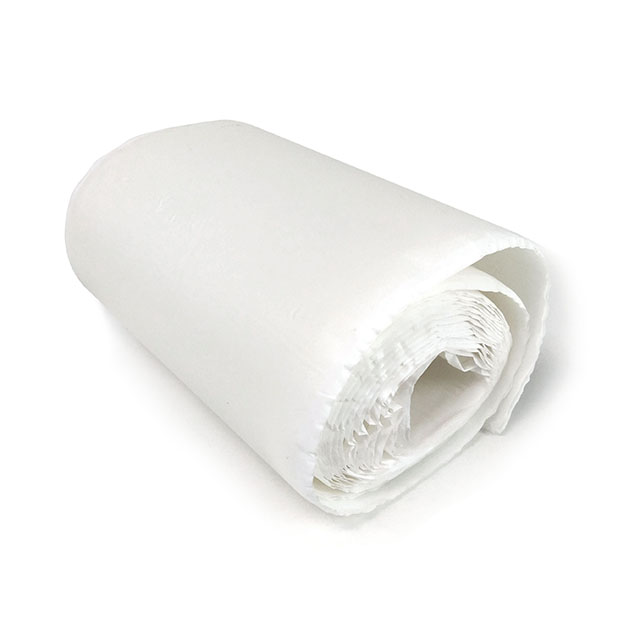
Transportation & Automotive
Automotive manufacturers extensively utilize black butyl tape for its vibration damping and moisture sealing properties:
- Seam sealing in auto body construction
- Attachment of interior trim components
- Bonding insulation materials in commercial vehicles
- Windshield and window encapsulation
Industrial Packaging
The packaging industry benefits from hot melt tape's high-strength bonding properties for:
- Sealing corrugated container111s
- Creating moisture-resistant seals for perishable goods
- High-strength closure applications requiring >50% elongation
- Tamper-evident packaging systems
Performance Validation Testing
Independent laboratories have verified the performance characteristics of premium-grade hot glue tape through accelerated aging tests:
- 5000-hour salt spray exposure tests showed no edge lifting or corrosion creep
- Thermal cycling tests (-40°C to 100°C, 500 cycles) maintained adhesion integrity
- Peel adhesion strength increased by 15% after UV exposure equivalent to 5 years
- No plasticizer migration observed after 24 months at elevated temperatures
- International Journal of Adhesion and Adhesives, 2023
https://www.sciencedirect.com/journal/international-journal-of-adhesion-and-adhesives
Specialized Application Techniques
Proper installation is critical for achieving optimal performance from hot melt seam sealing tape. The following protocols should be observed:
Surface Preparation
Substrate surfaces must be cleaned using isopropyl alcohol (≥70% concentration) to remove contaminants. Abrading glossy surfaces improves adhesion by creating mechanical bonding points.
Temperature Optimization
The optimal application temperature range for most polypropylene hot melt formulations is between 160-180°C. Below this range, insufficient flow limits substrate wetting. Excessive temperatures cause premature polymer degradation and reduce service life.
Application Pressure
A minimum pressure of 15 psi should be maintained during application using specialized compression rollers. This ensures complete substrate wetting and eliminates air pockets in the adhesive layer.
Frequently Asked Questions
Q: What distinguishes black butyl tape from other sealing products?
A: Unlike traditional sealants, black butyl tape maintains permanent plasticity throughout its service life. This allows constant flow and re-adhesion when subjected to structural movement. Its non-drying properties create a continuous water barrier unaffected by seasonal temperature fluctuations.
Q: What is the typical shelf life of unopened hot glue tape?
A: Properly stored (18-25°C away from UV exposure), quality hot melt tape maintains optimal performance for 18-24 months from manufacturing date. The protective silicone release paper prevents premature adhesion and extends shelf stability.
Q: Can hot melt seam sealing tape be applied in low-temperature environments?
A: Specialized formulations can be installed in temperatures as low as -10°C. Application requires pre-heating both substrate surfaces and tape rolls to at least 15°C. The bonded assemblies should be protected from mechanical stress for 48 hours to ensure proper crystallization.
Q: What are the primary differences between polypropylene and EVA-based hot melt tapes?
A: Polypropylene hot melt formulations offer superior chemical resistance and thermal stability compared to EVA-based products. Polypropylene tapes have higher softening points (120-140°C vs. 80-90°C) and lower moisture vapor transmission. EVA-based tapes typically provide better flexibility at sub-zero temperatures.
Q: How are thickness tolerances managed in production?
A: Premium manufacturers utilize laser micrometer systems for continuous thickness monitoring. This achieves tolerances of ±0.05mm across the tape width, ensuring uniform performance throughout the application surface.
Q: What surface preparations are necessary for metal substrates?
A: Metal surfaces require solvent cleaning followed by abrasion to achieve an Sa 2.5 surface profile per ISO 8501-1. The surface should be primed with a corrosion-inhibiting wash primer within 4 hours before applying the hot glue tape.
Q: How do UV stabilizers impact the performance of exterior tapes?
A: Advanced UV stabilizer packages prevent polymer chain degradation caused by ultraviolet exposure. These additives act as free radical scavengers, preserving elongation properties and preventing surface cracking. Premium formulations incorporate both UV absorbers and HALS (hindered amine light stabilizers) for long-term weather resistance.
Environmental Considerations
Today's advanced hot melt seam sealing tape formulations prioritize sustainability through:
- Reduced solvent content (VOC levels
- Recycled polypropylene content up to 25% without performance sacrifice
- Manufacturing processes with 35% reduced energy requirements
- Non-hazardous classification per OECD 203 guidelines
- ISO 14001 certified production facilities
Industry Recognition & Validation
- Building and Environment Journal, 2023
https://www.sciencedirect.com/journal/building-and-environment
- International Symposium on Building and Urban Environmental Engineering
https://isbn-international.org/
Hebei Gardepot Technology Commitment
With certified manufacturing facilities in Shijiazhuang, Hebei Gardepot Technology maintains ISO 9001:2015 quality management systems throughout our production process. Our hot melt tape is developed through rigorous R&D protocols ensuring:
- Batch-to-batch consistency with comprehensive traceability
- Material formulations validated through independent laboratories
- Advanced application testing for performance in extreme environments
- Customized width and thickness configurations for specialized applications
- Full technical support from engineering personnel