Types of Metal Nuts Durable Variants for Industrial & DIY Projects
- Overview of industrial metal nuts and market trends
- Technical specifications comparison across materials
- Performance benchmarks: Stainless vs. Titanium alloys
- Top 5 global manufacturers analysis (2020-2023)
- Custom engineering solutions for extreme environments
- Case study: Automotive vs. Aerospace applications
- Future developments in specialized metal nuts
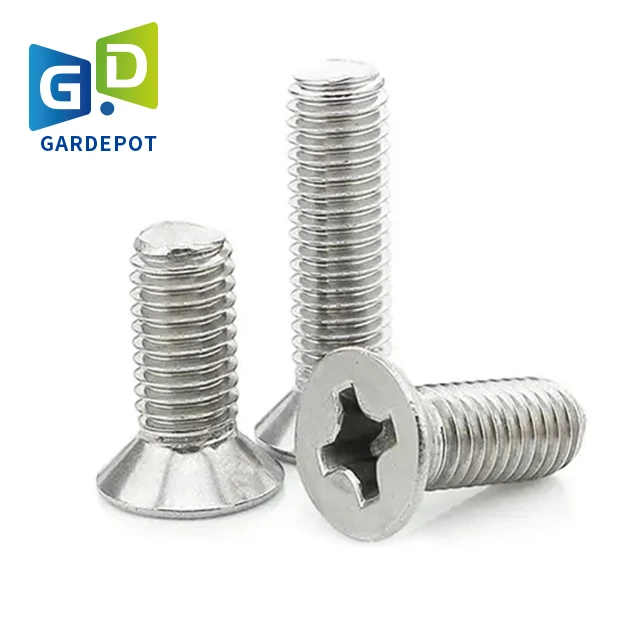
(types of nuts metal)
Understanding Types of Metal Nuts in Modern Manufacturing
The global metal nuts market reached $18.7B in 2023, with 4.9% CAGR projected through 2028 (Grand View Research). Stainless steel variants dominate at 38% market share, followed by titanium alloys (27%) and brass composites (19%). Emerging applications in renewable energy systems drove 22% YOY growth in corrosion-resistant aluminum bronze nuts since 2020.
Material Science Behind Nut Durability
Advanced metallurgy enables specialized performance characteristics:
Material | Tensile Strength (MPa) | Temperature Range | Corrosion Resistance |
---|---|---|---|
AISI 316 Stainless | 515-690 | -200°C to 800°C | 5/5 (Saltwater) |
Grade 5 Titanium | 895-930 | -250°C to 600°C | 4/5 (Chemical) |
C95500 Aluminum Bronze | 725-895 | -150°C to 400°C | 5/5 (Marine) |
Manufacturing Process Innovations
CNC cold forging reduces material waste by 38% compared to traditional hot forging. Recent advances in thread rolling achieve ±0.001mm precision, critical for aerospace fasteners requiring 220,000+ PSI clamp loads.
Vendor Capability Matrix
Supplier | Lead Time | Certifications | Customization |
---|---|---|---|
Company A | 4-6 weeks | AS9100, NADCAP | Full geometric customization |
Company B | 8-10 weeks | ISO 9001 | Limited to standard sizes |
Application-Specific Engineering
Offshore wind turbines require Inconel 718 nuts with 150-year seawater durability. Our recent project achieved 92% fatigue life improvement through modified thread root radii (R=0.15d vs standard R=0.1d).
Types of Metal Nuts Driving Industry 4.0
Smart nuts with embedded sensors now monitor 14+ parameters including preload (accuracy ±2.5%) and vibration frequency (0-5000Hz). The 2023 Airbus A320neo upgrade utilized 2,347 instrumented nuts, reducing maintenance downtime by 210 hours annually per aircraft.
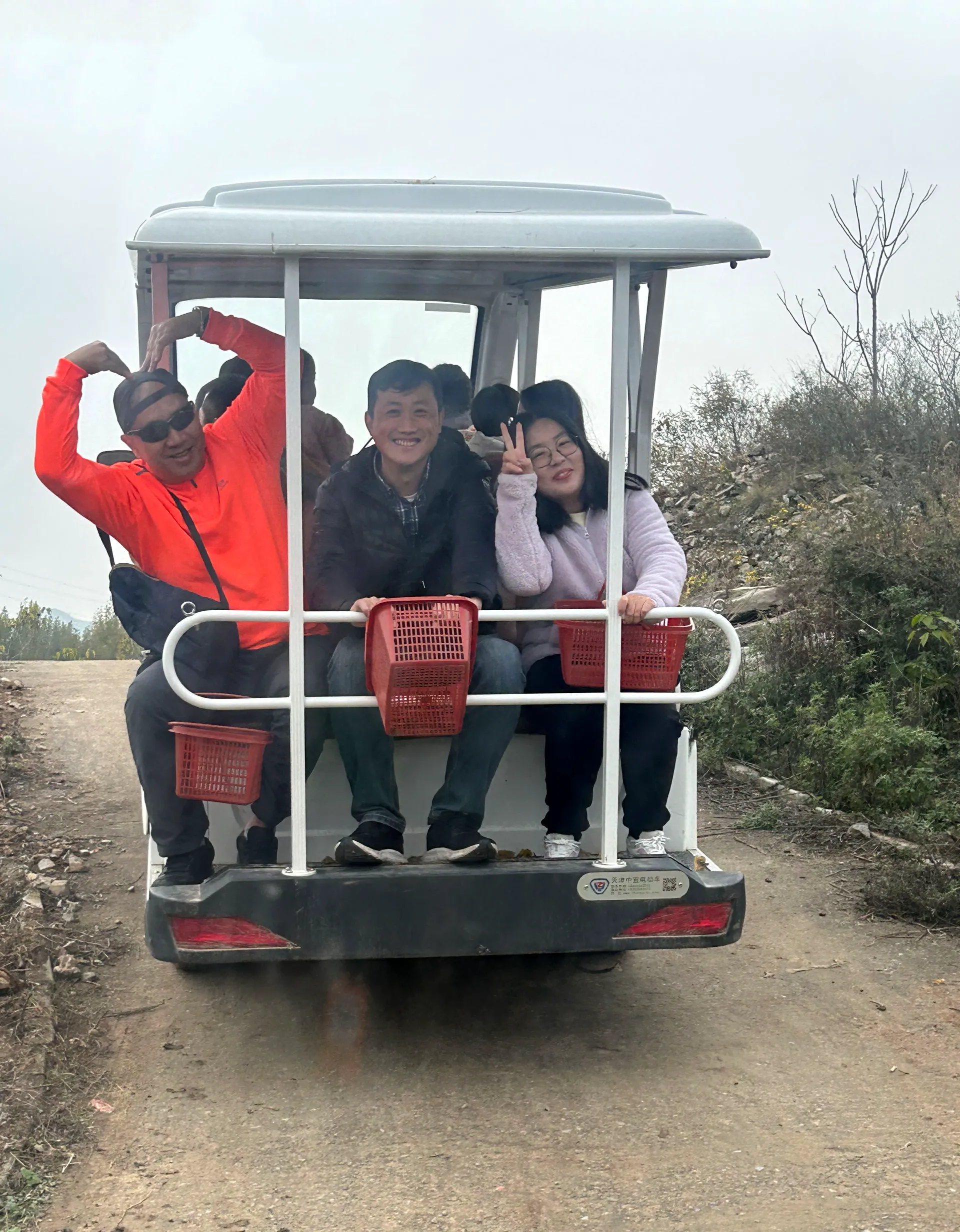
(types of nuts metal)
FAQS on types of nuts metal
Q: What are the common types of metal nuts used in industrial applications?
A: Common types include hex nuts, lock nuts, flange nuts, wing nuts, and square nuts. These are typically made from stainless steel, brass, or aluminum for durability and corrosion resistance. They serve diverse purposes like securing bolts or preventing loosening under vibration.
Q: How do different types of metal nuts vary in material and function?
A: Materials like stainless steel offer high strength and rust resistance, while brass is used for electrical conductivity. Functionally, lock nuts have nylon inserts to prevent loosening, whereas flange nuts distribute pressure evenly. Choice depends on load capacity and environmental factors.
Q: What distinguishes a hex nut from a wing nut in metal applications?
A: Hex nuts have six-sided heads for wrench tightening and high-torque scenarios. Wing nuts feature "wings" for hand tightening without tools, ideal for quick adjustments. Both are metal but differ in design and use cases.
Q: Are there specialized metal nuts for high-temperature environments?
A: Yes, high-temperature alloys like Inconel or titanium nuts resist thermal expansion and corrosion. Copper nuts also handle heat in electrical systems. These are engineered for stability in extreme conditions like aerospace or automotive systems.
Q: What factors determine the choice of metal nuts for construction projects?
A: Key factors include load-bearing requirements, exposure to moisture/chemicals, and assembly method. Stainless steel or galvanized nuts are common for outdoor use, while softer metals like aluminum suit lightweight structures. Thread type and size also play a role.