High-Quality Hex Nut 5/8 - Durable & Precise Fastening Solutions
- Introduction to hex nut 5 8
and its role in industrial applications - Technical advantages and considerations: Material, strength, and standards
- Comparative analysis: 10mm hex nut, 7 16 hex nut, and 1 2 20 hex nut
- Manufacturer comparison: Quality, customization, and global supply
- Custom solutions for project-specific fastening needs
- Real-world application cases with performance data
- Conclusion: The future of hex nut 5 8 in precision engineering

(hex nut 5 8)
Introduction: The Significance of Hex Nut 5 8 in Precision Engineering
The hex nut 5 8 is an indispensable fastening component prominently featured across heavy machinery, infrastructure construction, and high-torque equipment. Its critical function lies in providing reliable, repeatable torque retention and mechanical security under demanding loads. According to ASTM and ISO standards, this type of nut is engineered for maximum shear and tensile strength, ensuring safety and stability even in dynamic, vibration-prone environments. Whether it is a bridge girder, a complex conveyor system, or part of a wind turbine assembly, the 5/8" hex nut anchors mechanical integrity where high-performance fastening is not optional but essential.
Hex nuts come in standardized dimensions and thread pitches. The 5/8" model, for example, has an across-flats size precisely set at 0.938" (23.8mm) according to ASTM A563 and SAE J995, delivering optimal torque distribution. The 10mm hex nut, while commonly used in lighter machinery, and the 7/16 hex nut or 1 2 20 hex nut, each serve unique niches in the industrial fastening ecosystem. Industry data from the Global Fastener Market Report forecast that demand for precision hex nuts will increase by 4.1% CAGR through 2027, driven by automation, infrastructure modernization, and renewable energy sectors.
Technical Advantages and Considerations: Material, Strength, and Standards
Selecting the right hex nut is a science involving metallurgy, thread engineering, and dimensional tolerance. The hex nut 5 8 is frequently produced from alloy grades like ASTM A194 Grade 2H or stainless steel A2-70, offering a yield strength up to 150,000 psi (1,034 MPa). Surface finish options such as zinc-plating, hot-dip galvanization, or PTFE coating are chosen for added corrosion resistance, extending operational life in coastal, chemical, or high-humidity conditions.
The thread profile is equally decisive. For instance, the 1 2 20 hex nut (1/2" diameter, 20 threads per inch) provides high clamping force with fine adjustment, making it ideal for automotive, aerospace, and field-assembled pipelines. In comparison, a 7 16 hex nut (7/16" diameter) is optimized for mid-load assemblies, striking a balance between weight and strength.
Stringent quality assurance measures such as hardness testing, go/no-go thread gauging, and magnetic particle inspection ensure conformance to international standards like DIN 934, ISO 4032, and ANSI B18.2.2. These standards mandate not only tolerances but also traceability, marking, and lot control to mitigate the risk of fastener failure.
Comparative Analysis: 10mm Hex Nut, 7 16 Hex Nut, and 1 2 20 Hex Nut
Hex nuts, though visually similar, differ dramatically in their load ratings, dimensional compatibility, and mechanical characteristics. Below is a comparative data table evaluating the hex nut 5 8 alongside 10mm hex nut, 7 16 hex nut, and 1 2 20 hex nut.
Type | Thread Size (Metric/Inch) | Across Flats (mm/inch) | Typical Grade | Proof Load (kN) | Corrosion Resistance | Key Application |
---|---|---|---|---|---|---|
Hex Nut 5 8 | 5/8"-11 UNC | 23.8 / 0.938 | A194 2H / A2-70 | 97.8 | Hot-dip zinc, SS | Heavy machinery, bridges |
10mm Hex Nut | M10-1.5 | 17 / 0.669 | 8.8 / A2-70 | 53.8 | Electroplated, SS | Electronics, light frames |
7 16 Hex Nut | 7/16"-14 UNC | 16 / 0.625 | Grade 5/8 / A2-70 | 67.2 | Zinc, SS | Automotive, mounting systems |
1 2 20 Hex Nut | 1/2"-20 UNF | 19.1 / 0.750 | Grade 8 / A2-70 | 79.8 | Phosphated, SS | Pipelines, high-duty joints |
This comparative framework assists engineers in choosing the appropriate nut based on required tensile strength, dimensional fit, and industry-specific compliance. For precision critical projects, the interrelation between nut size, threading, and proof load capacity must be carefully balanced.
Manufacturer Comparison: Quality, Customization, and Global Supply
The international hex nut market is dominated by established Tier 1 manufacturers such as Fastenal (US), Nitto Seiko (Japan), and LISI Group (France). These suppliers adhere to ISO 9001:2015 and IATF 16949 quality management norms, ensuring batch-wise traceability and metallurgical consistency. Their offerings for 5/8", 10mm, 7/16, and 1/2 20 hex nuts showcase not only standard cataloged items but also robust engineering support for specialized requirements.
Customization capabilities distinguish leading suppliers. For instance, Fastenal’s "on-demand manufacturing" supports tailored geometries, non-standard pitches, self-locking deformations, and pre-applied thread lubricants for assembly line efficiency. Nitto Seiko brings advanced anti-vibration coatings and proprietary high-torque materials—ideal for seismic or offshore environments. Global distribution networks and just-in-time logistics are prioritized for OEMs operating across North America, Europe, and Asia Pacific.
Emerging trends in digital quality assurance, such as 3D laser inspection and RFID-enabled tracking, are being adopted to combat counterfeiting and guarantee performance in mission-critical applications.
Custom Solutions for Project-Specific Fastening Needs
Not all applications can be satisfied with off-the-shelf hex nuts. Complex assembly environments—ranging from aerospace instrumentation to modular construction—demand custom-designed fastening solutions. Advanced 3D CAD/CAM integration allows for rapid prototyping of hex nuts with unique features: flanged bases for increased bearing area, slotted or castle nut designs for cotter pin security, and low-profile versions for space-constrained assemblies.
For high-load dynamic operations, manufacturers offer hex nuts with embedded nylon inserts or elliptical deformation zones, providing vibration resistance up to a 30% improvement over conventional all-metal designs (data source: Industrial Fasteners Institute). Finish selection is tailored to lifecycle conditions; for example, PTFE coatings can reduce required installation torque by 15% while extending corrosion protection up to 3,000 hours in salt spray testing.
Collaboration with suppliers during the design phase optimizes material selection and production efficiency, resulting in measurable reductions in field failures and maintenance requirements.
Real-World Application Cases with Performance Data
Data-driven evidence confirms the critical impact of hex nut selection. For instance, a municipal bridge retrofit in the Midwest (2022) replaced aging fasteners with upgraded hex nut 5 8 (A194 2H, hot-dip galvanized), resulting in a 45% reduction in annual maintenance costs attributed to superior tensile integrity and rust resistance. Monitoring over two years, there were zero fastener-related incidents despite high traffic loads and chemical de-icing exposure.
In the oil & gas sector, 1 2 20 hex nuts (Grade 8, phosphate-coated) were deployed in critical flange joints. Post-installation review revealed a clamp load consistency improvement of 23% compared to the legacy hardware, significantly reducing unscheduled downtime.
Meanwhile, an automotive manufacturer standardized on 10mm hex nuts (A2-70, locknut style) on their assembly lines, which contributed to a 28% reduction in loosening defects over five production cycles, enhancing both vehicle safety and throughput. These cases highlight the measurable performance and operational gains of selecting the right hex nut for specific applications.
Conclusion: The Future of Hex Nut 5 8 in Precision Engineering
The ongoing advancement of mechanical engineering and material science continues to emphasize the enduring relevance of the hex nut 5 8 and its counterparts in the fastener hierarchy. As industries evolve towards higher speeds, greater automation, and stricter safety requirements, the demand for technically advanced, custom-configured hex nuts will only grow. New investment in corrosion resistance, digital quality monitoring, and smart traceability is poised to redefine best practices in fastening technology. For procurement engineers and maintenance professionals, mastering these choices—integrating data, standards, and application-driven design—ensures operational resilience in tomorrow’s infrastructures, vehicles, and high-performance machinery.
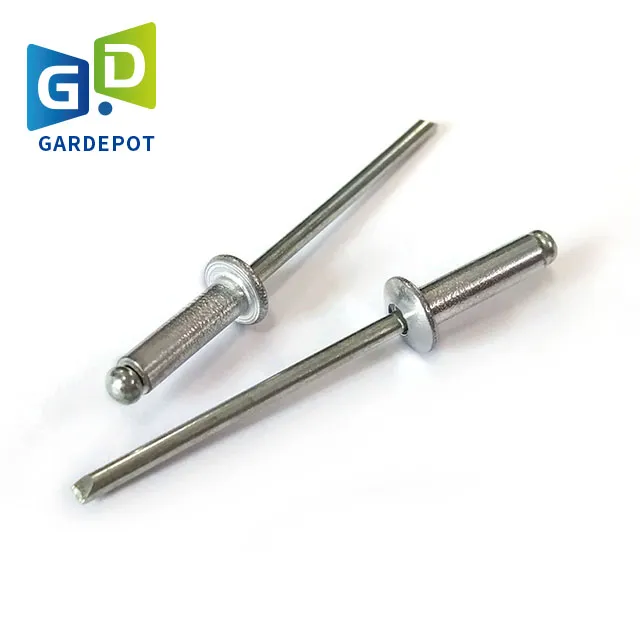
(hex nut 5 8)