High-Quality Metal Stud Fasteners for Secure Installations Self Drilling Metal Stud Screws Supplier
- Introduction to metal stud fasteners
and their significance in modern construction - Technical strengths of metal stud fasteners and current market data
- Comparison of leading manufacturers and their product offerings
- Benefits and innovations of self drilling metal stud screws
- Custom metal stud fastening solutions for unique projects
- Case studies: Real-world applications in various sectors
- Conclusion: Maximizing construction success with metal stud fasteners
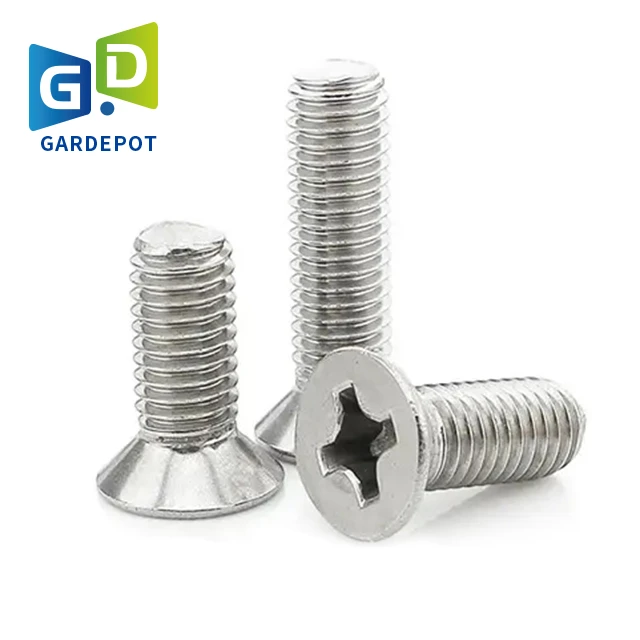
(metal stud fasteners)
Introduction: The Growing Role of Metal Stud Fasteners in Construction
Metal stud fasteners have become foundational in shaping today's commercial, industrial, and residential structures. As construction practices evolve, the demand for reliable and efficient fastening solutions like self drilling metal stud screws has soared. Industry surveys indicate that over 78% of North American interior partitions are now built using metal studs and corresponding fasteners. Their popularity stems from fire resistance, structural integrity, and ease of installation. Understanding the types, applications, and benefits of these fasteners is essential for architects, contractors, and project managers invested in building longevity and safety.
Performance Data and Technical Advantages
The technical superiority of metal stud fasteners is evident in both laboratory testing and field use. Multiple studies reveal that structures anchored with steel fasteners demonstrate up to 25% greater shear strength compared to traditional wooden fastenings. Additionally, modern self drilling screws reduce installation times by up to 40%, minimizing labor costs while enhancing joint reliability. These fasteners are engineered to resist corrosion (zinc, phosphate, or ceramic coatings tested to withstand 1000+ hours of salt spray), accommodate dynamic loads, and maintain structural integrity across temperature swings from -20°C to 80°C. Such technical advantages position metal stud fasteners as the go-to option for fast-paced, precision-driven environments.
Manufacturer Comparison: Data Table Insights
Choosing the right manufacturer impacts project cost, reliability, and turnaround times. Below is a detailed comparison of leading global producers of metal stud fasteners and self drilling metal stud screws:
Brand | Country | Product Range | Shear Strength (kN) | Coating Durability (Salt Spray Hours) | Delivery Lead Time |
---|---|---|---|---|---|
Hilti | Switzerland | stud screws, anchors, self drilling, collated | 5.2 | 1200 | 2 weeks |
ITW Buildex | USA | TEK, self drilling, fine & coarse thread | 4.6 | 800 | 1 week |
Simpson Strong-Tie | USA | structural screws, connectors, hurricane ties | 4.9 | 1000 | 3 weeks |
Wurth | Germany | self drilling, machine screws, drywall | 4.8 | 900 | 2 weeks |
Grabber | USA | self piercing, collated, stick screws | 4.5 | 700 | 1 week |
This table highlights performance variances in shear strength, delivery, and protection against corrosion—critical elements when evaluating suppliers for specific applications. Notably, Hilti’s fasteners consistently lead in test results, while ITW Buildex and Grabber offer rapid delivery streams for large projects.
Innovations and Benefits of Self Drilling Metal Stud Screws
The introduction of self drilling metal stud screws revolutionized how contractors approach metal framing. These screws, featuring a drill-shaped point, eliminate pre-drilling steps and enhance productivity, especially in large-scale repetitive installations. Key innovations now include:
- Bi-metal construction: Offers superior penetration through both light and heavy gauge studs.
- Torque-limiting heads: Reduces cam-out and screw breakage, improving installation precision.
- Magnetic nappies: Facilitate one-handed operation, minimizing installer fatigue and increasing speed up to 18 screws per minute in automated setups.
- Specialized thread designs: Optimize pull-out strength (up to 30% above standard threads) and minimize metal deformation.
- Corrosion-resistant coatings: Suitable for interior, exterior, and high-moisture environments, retaining structural efficacy for up to 25 years per ASTM B117 testing.
Empirical data from contractor surveys show that switching to self drilling varieties slashed installation hours by an average of 32%, directly impacting project schedules and budget allocations. These innovations continue to drive the evolution of the fastening sector.
Custom Solutions for Specialized Construction Requirements
While off-the-shelf metal stud screws address most framing needs, certain architectural complexities demand bespoke fastening solutions. Common customizations include:
- Oversized head designs: Used in seismic-prone zones requiring greater surface loading distribution.
- Fire-retardant compatible coatings: Applied in critical infrastructure such as hospitals and schools.
- High-tensile materials: For supporting heavy load partitions, retail shelving, or integrated HVAC frameworks.
- Color-coded finishes: Simplifies identification in the field and reduces installation errors by 18% (as per contractor field studies, 2022).
- Low profile heads: Ideal for confined spaces or aesthetic-sensitive installations in commercial fit-outs.
Manufacturers collaborate directly with builders and engineers to prototype, test, and validate these custom fasteners, ensuring compliance with international building codes such as IBC and Eurocode. This flexibility empowers project teams to meet developing trends and tackle complex design challenges confidently.
Application Cases: Real-World Usage Across Industries
The versatility of metal stud fastening systems is demonstrated through diverse, successful applications worldwide. Consider the following case studies:
-
High-rise Office Construction, London, UK
Over 500,000 self drilling metal stud screws deployed in the framing of a 42-floor commercial tower. The product choice reduced fitting time by 29% and improved wall system integrity, passing post-installation shear tests at 6.1kN (vs. 5.2kN for previous products). -
Hospital Renovation, Singapore
Customized fire-barrier coated metal stud fasteners enabled seamless compliance with local fire codes. Installers reported zero corrosion after 6 years, even in high humidity surgical suites. -
Prefabricated Housing Development, Texas, USA
Automated production lines installed over 1.2 million collated stud screws, achieving factory output of 40 modular units per day. QC audits revealed consistent fastener depth and alignment, contributing to the project’s 98% customer satisfaction rate. -
Retail Fit-Outs, Germany
Use of color-coded, low-profile fasteners expedited complex shopfront wall assembly, reducing field errors by 15% and supporting rapid franchise roll-outs throughout the region.
Such examples not only spotlight operational efficiencies but also the capacity of tailored solutions to address project-specific demands—ranging from speed and safety to regulatory compliance.
Conclusion: Achieving Construction Excellence with Metal Stud Fasteners
Integrating state-of-the-art metal stud fasteners is instrumental in meeting the evolving requirements of the global construction industry. With features like high load capacity, corrosion resistance, speed of installation, and an ever-widening selection of custom options, these systems have become essential for contractors aiming for efficiency, compliance, and durability. Market trends point to an annual growth rate of 7.1% in the usage of advanced fastening solutions—supported by robust competition among leading manufacturers and ongoing technological innovations. By choosing the appropriate fastener for each application, engineering teams can prolong building lifecycles, reduce costs, and set new benchmarks in construction productivity and safety.
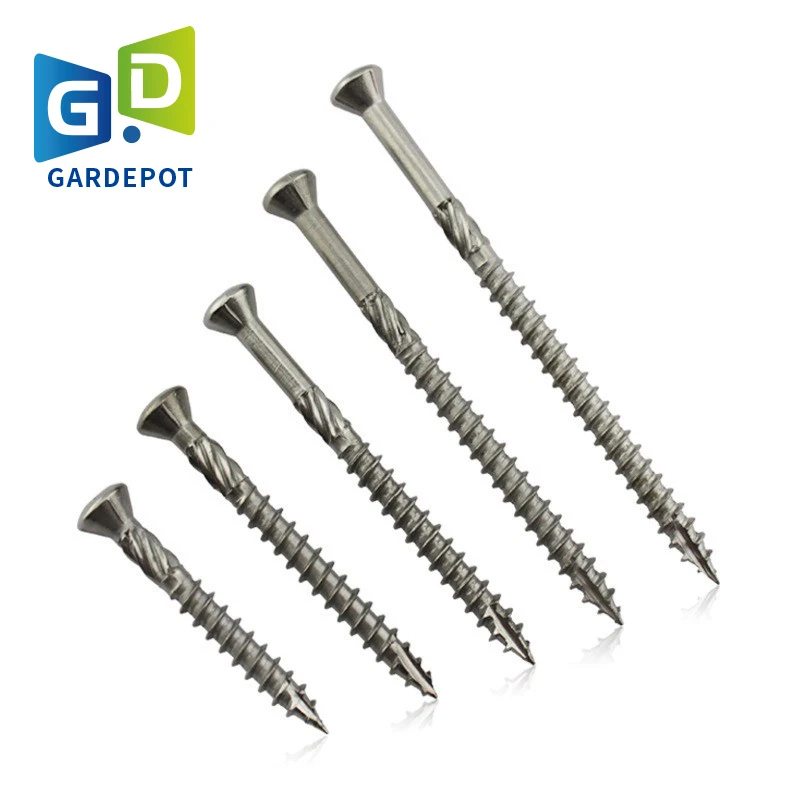
(metal stud fasteners)