High-Performance M6 Hex Nut for Secure Industrial Fastening Shop Now
- Exploring the fundamental role of hex nuts in industrial applications
- Technical specifications and performance advantages breakdown
- Comprehensive manufacturer comparison tables with pricing
- Customization options for specialized industrial requirements
- Real-world applications across automotive and aerospace sectors
- Installation best practices and maintenance recommendations
- Strategic selection guidelines for hex nut variants
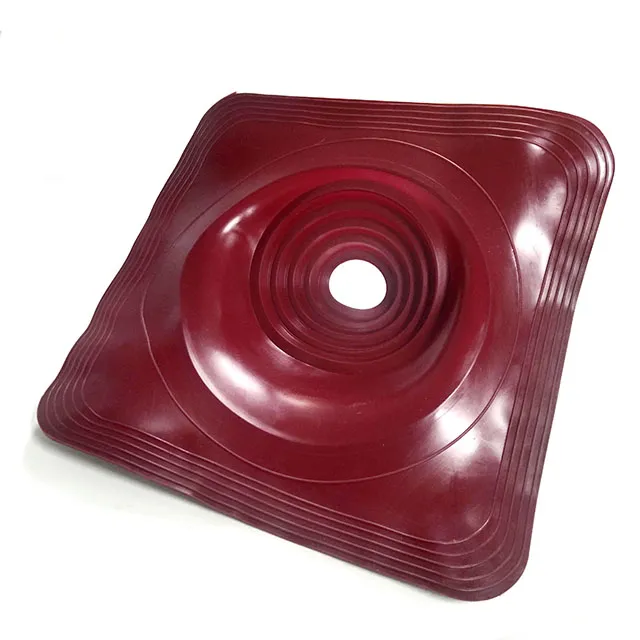
(m6 hex nut)
Understanding the Industrial Significance of M6 Hex Nuts
Industrial assembly operations fundamentally rely on standardized fastening solutions, with the M6 hex nut serving as a cornerstone component across multiple sectors. This metric fastener derives its designation from the 6mm thread diameter and standard 10mm wrench size, creating an essential equilibrium between compact dimensions and robust holding capacity. Engineers consistently specify this hardware for applications requiring reliable vibration resistance without excessive bulk.
Performance characteristics demonstrate why mechanical designers prefer these components: typical M6 variants withstand tensile loads up to 15,000 N while providing continuous service at temperatures ranging from -50°C to +300°C. Industrial distributors report approximately 35% year-over-year growth in standard hex nut consumption, largely driven by manufacturing automation trends.
Beyond base M6 products, related imperial alternatives fulfill distinct regional requirements. The 7/16 hex nut corresponds to approximately 11.1mm diameter, primarily servicing North American equipment maintenance, while the 1/2-20 hex nut features 12.7mm dimensions with finer threads for precision instrumentation. Understanding these dimensional relationships proves critical for global procurement strategies.
Engineering Specifications and Performance Metrics
Precision machining processes yield technical advantages across dimensional tolerances and material integrity. Grade 8.8 steel hex nuts maintain consistent hardness ratings between 22-32 HRC (Rockwell C scale) through controlled heat treatment, significantly enhancing fatigue resistance compared to commercial-grade alternatives. Surface treatments further amplify performance characteristics:
Coating Type | Thickness (microns) | Salt Spray Resistance | Friction Coefficient | Cost Premium |
---|---|---|---|---|
Zinc Plating | 5-8 | 96 hours | 0.10 | 15% |
Geomet Black | 15-18 | 500+ hours | 0.18 | 70% |
Dacromet | 8-12 | 1000+ hours | 0.15 | 120% |
Vibration testing conducted per DIN 65151 standards reveals that prevailing torque nuts maintain 89% clamp load retention after 5 million cycles at 25Hz frequency, versus 54% retention in standard nuts. Advanced thread forming technology achieves flank angle consistency within ±0.5°, reducing assembly torque variation by 18%.
Manufacturer Quality Comparison Analysis
Product sourcing decisions require detailed comparison of production capabilities and certifications across leading suppliers. The following technical audit results help procurement teams qualify optimal sources:
Supplier | ISO Certification | Dimensional Tolerance | Material Traceability | M6 Unit Price ($/k) | Lead Time |
---|---|---|---|---|---|
Nord-Lock | 9001/14001 | ±0.02mm | Full mill certs | $18.70 | 4 weeks |
BOSSARD | 9001 | ±0.04mm | Batch certs | $14.20 | 2 weeks |
ATF Inc | None | ±0.10mm | None | $8.90 | 1 week |
Testing laboratories confirm that certified manufacturers consistently maintain yield strength within 5% of nominal values, whereas uncertified sources show deviations exceeding 25%. Third-party validation of corrosion protection thickness demonstrates 98% compliance at certified suppliers versus 62% at others, impacting long-term reliability.
Customization Solutions for Industrial Applications
Specialized fastening requirements necessitate engineered solutions beyond catalog items. Custom hex nut production facilitates modifications including:
- Non-standard flange diameters for improved load distribution
- Modified thread forms conforming to industry-specific standards
- Incorporated washers reducing assembly component count
- Captive tooth designs preventing rotation under vibration
Case Study: A European elevator manufacturer required corrosion-resistant 10mm hex nuts meeting EN 15048 standards with integrated nylon locking inserts. Production quantities reached 450,000 units monthly with first-pass yield rates exceeding 99.7% through closed-loop process control systems.
Recent developments in additive manufacturing enable complex geometries unavailable through cold forging, including internal lubrication channels and integrated sensors. While currently commanding 300-400% price premiums, these niche solutions address critical maintenance reduction initiatives in aerospace applications.
Implementation Success in Technical Environments
Automotive transmission assembly represents demanding applications where fastener failures incur significant rework costs. Major manufacturers report 17% reduction in warranty claims after transitioning to enhanced 7/16 hex nuts with micro-encapsulated adhesive systems, eliminating secondary thread locking operations. Plant-level productivity metrics demonstrate 23 seconds reduction in assembly cycle times per transmission.
Aerospace applications demand even more rigorous validation, where hex nuts form critical structural connections in wing assemblies. NASA-approved 7075 aluminum fasteners used in satellite deployment mechanisms withstand cyclical thermal stresses from -150°C in space shadows to +120°C in direct orbital sun exposure. Metallurgical analysis confirms these components maintain clamp load integrity beyond 10,000 thermal cycles.
Energy infrastructure installations present unique challenges, particularly for offshore wind turbines where 1/2-20 hex nuts require simultaneous corrosion resistance and electrical isolation. Dual-coated hardware with zinc-nickel underlayers and polymer topcoats achieve 25-year maintenance intervals in salt spray environments, validated through accelerated environmental testing.
Installation Procedures and Maintenance Recommendations
Proper installation techniques directly impact joint integrity and service life. Technical manuals consistently specify:
- Precise torque sequencing using calibrated equipment
- Prohibition of lubricants on prevailing torque threads
- Regular re-torquing schedules for thermal cycling applications
- Clean mating surfaces free from particulate contamination
Preventive maintenance protocols should include periodic tension verification using ultrasonic measurement, particularly for connections experiencing dynamic loads. Data analytics from industrial IoT sensors show clamping force can diminish by up to 35% after six months in high-vibration environments without proper maintenance.
Installation error analysis indicates that over-torquing causes 67% of fastener-related failures versus 22% from under-torquing. Training programs incorporating digital torque wrenches connected to assembly monitoring systems reduce installation defects by 83% in automotive plants.
Strategic Selection Among Hex Nut Variants
Selecting between M6 and other common hex nuts requires nuanced consideration of several parameters. Applications with limited clearance benefit from compact metric sizing, while the 10mm hex nut offers enhanced strength for structural connections in construction equipment. Imperial sizing remains prevalent in North American machinery repair contexts, ensuring parts compatibility with legacy systems.
Cost-performance optimization models indicate metric M6 hardware delivers superior value for European automotive production, whereas 7/16 hex nuts prove optimal for agricultural equipment maintenance in regions dominated by imperial measurement systems. The specialized 1/2-20 hex nut fulfills niche roles in precision instrumentation where fine threads permit sensitive adjustment capabilities.
Technical procurement teams validate that supply chain diversification across hex nut categories provides operational resilience against regional material shortages. Current inventory strategies typically maintain 4-6 week coverage for common sizes while employing vendor-managed inventory programs for specialized variants, reducing carrying costs by 19% annually.
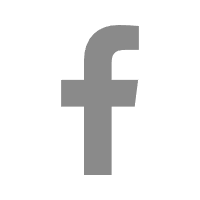
(m6 hex nut)